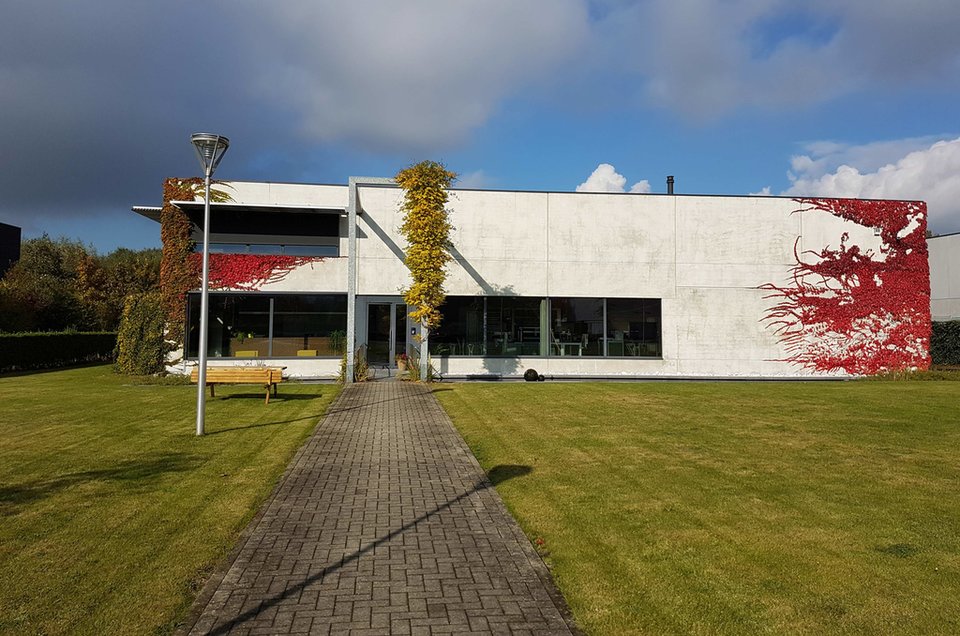
COMPANY INSIGHT
Sponsored by: NUCOMAT
Nucomat – your partner in lab automation
Automated sample preparation and testing is key in order to further improve operator safety, increase lab productivity and quality of data in mining laboratories.
S
ince its inception, Nucomat – the name is combination of ‘nuclear’ and ‘automation’ – has grown and adapted to market demand. The business originally specialised as a system integrator for the laboratory sector, and evolved to provide custom-built solutions to suit specific needs and workflows. Founder Noël Van de Steene discusses the company’s progress.
Why did you form Nucomat?
About 40 years ago, after studying industrial automation, I started my career in the nuclear sector, which was still big at the time.
The company I worked for was headquartered in the US. After a few years, it decided to pull the plug on the Belgian team in 1988. This was an opportunity for me and some colleagues to found our own company and convert our previous employer into our first customer.
Our introduction to the laboratory world came seven years later. We started with small systems and gradually increased the size of projects over time. Originally, we were three people; now our team has grown to 20.
As the company grew, so did our knowledge. Some 33 years later, I can look back on a wide portfolio of systems in the biochemical, oleochemical, food, personal care, pharma, mining and recycling industries.
How did you get into the mining industry?
You could say we rolled into this business.
We did some projects for BASF and Solvay in Belgium, mainly covering automation of sample preparation for quality control samples. There was no off-the-shelf solution for automating the complete sample workflow before analysis, and the industry was looking for companies that could offer this.
The mining industry found us in 2003. Phelps Dodge, now known as Freeport-McMoRan, wanted to automate its laboratories in Arizona. Nucomat installed seven Wetchem systems, some of which remain operational to this day. We have since carried out multiple mining projects across the world.
How has the mining lab industry evolved in the last 20 years?
Mining is a challenging sector. Production sites and laboratories are often located in remote locations, and it is hard labour with some severe risks for personnel.
Risk awareness is the biggest shift in mining. The focus is on safety! Not only on the production site but also in the laboratories where technicians need to work with hazardous chemicals. Interest in automation has increased significantly.
Quality of analysis results is becoming more important. Traceability and repeatability have become key, and automation delivers on these values. As an example, sample preparation is traditionally performed manually using volumetric flasks because it’s easier than weighing. Unfortunately, it is also less accurate. This is a key area where automated systems can improve quality.
On a global scale, the importance of recycling and environmental concerns is growing. We also receive inquiries for ‘city mining’ – recycling of precious metals. As in many other industries, mining is also seeing a shift to a circular economy.
What main systems is Nucomat developing?
We have multiple systems for different industries. For mining, we mainly focus on automating wet chemistry. We start from an unknown sample and deliver a validated result. The start sample can be pulverised rock, pellets, liquids, slurries or aqueous solutions.
We have developed systems to analyse a wide variety of products:
- Base metals: copper, lead, nickel and zinc;
- Precious metals: silver, gold, platinum, palladium;
- Molybdenum;
- Quality of waste water.
The samples could be from different places – blast holes or geological samples – but also from various steps in the production process such as untreated material or leach solution.
All our systems are modular; we connect a set of devices using a gantry robot to perform all operations for a specific application. This enables us to provide systems tailored to customers’ requirements using proven technology. Some of our systems have integrated instruments, while others provide processed samples for offline analysis.
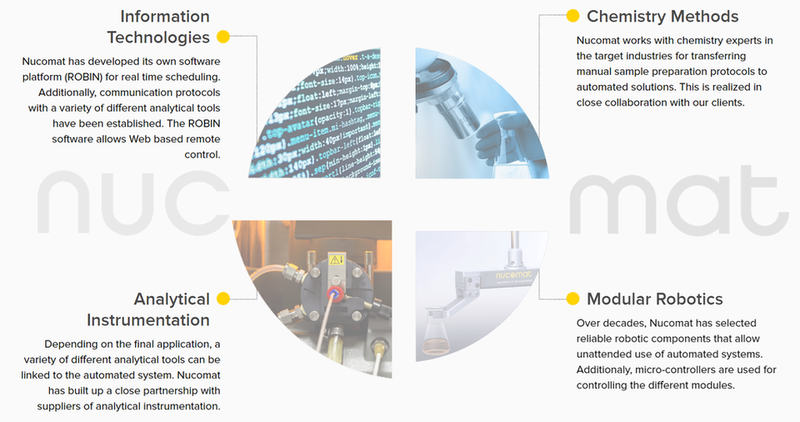
What is the main driver for choosing automation over manual labour?
The biggest gain is the increase in safety and quality. Automated systems will dispense, heat and transport dangerous acids. As a result, the risk for laboratory personnel is minimised.
Increased accuracy, traceability and reproducibility are the quality-related benefits. Machines can also run 24/7, making analyses less dependent on people.
What is Nucomat’s key to success?
We have been active in mining for almost 20 years. During that time, we have been able to validate and optimise our systems. Our history of successful projects means we can offer the right solution for customers.
Our systems have a lifespan of 10 years; some have more than 13 years of duty, and counting. They are designed so they will not go completely down if, for example, one powder sample is in error. If you have a second sampler on the system, the machine will continue operation. The same applies for a sample with a damaged label or tag. The system will put the sample aside and continue operation.
We always work in close collaboration with the customer, as they are the experts in their methods. We can also fall back on a wide network of consultants to assist us with specific, complex topics.
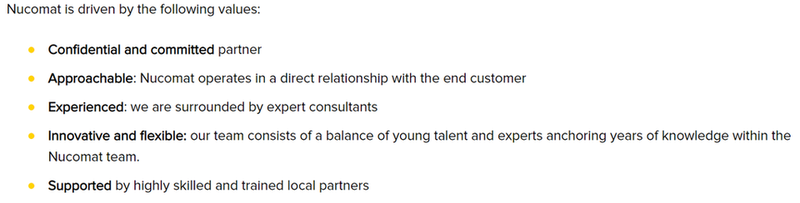
Nucomat is headquartered in Lokeren, Belgium, but you operate globally. How do you manage this?
We have several options to address service on a global level. In Belgium we have an experienced team who can give remote support. As our products are web based, we can identify issues and support customer via remote connection. In our experience, with the remote support and adequate training, local technicians can solve any issue.
Nucomat also offers service contracts, including remote support. A second part is preventive maintenance; once a year our technicians will inspect and maintain the complete system. Some local dealers offer support on Nucomat machines, such as Geo Assay in Chile and Thermo Techno in Russia. Having reliable partners in various locations makes this possible.
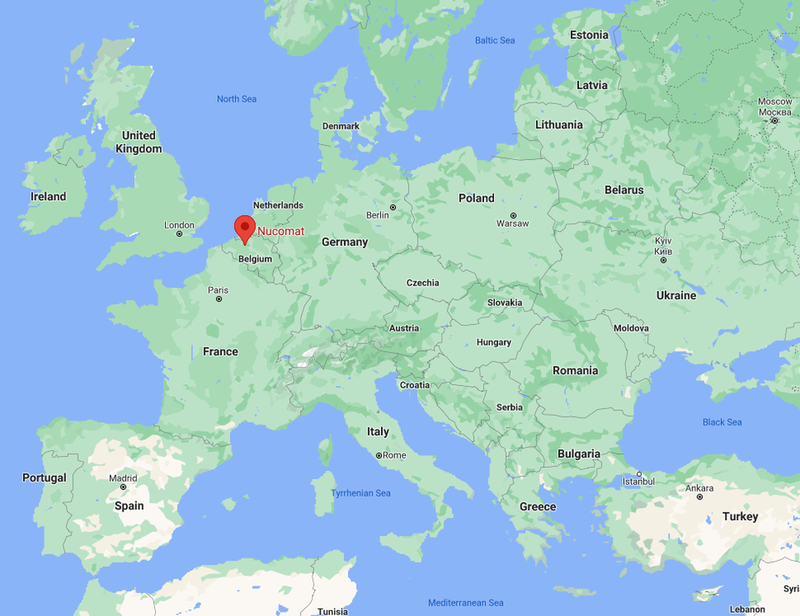
Where would I use one of your systems?
There are a couple of things to keep in mind which will make the step to automation easier. But even without these points, automation can still be an option.
- Mining sites analysing own samples;
- High accuracy requirement;
- High amounts of samples to run;
- Solid demand with quick turnaround times;
- Labs where instant result availability is required;
- Labs where system availability is key;
- Remote locations where lab chemists are hard to find.
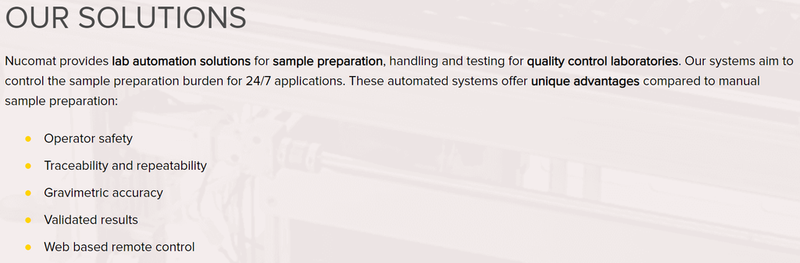
How is Nucomat preparing for the future?
The focus is on continuity:
- Preparing the next generation to run the company;
- Extending partnerships with current and new partners;
- Improving our knowledge;
- Keeping core technology in house, making us independent to external parties.
Covid brought the worldwide economy to a stop. We expect the business to start booming once the pandemic is over.
Last year most of our time was invested in developing the Compact Sample Preparation Unit. This modular automated unit is able to dispense up to four different liquids and perform digestions. It is possible to add a ColdBlockTM digester to the unit to do the digestions with active cooling. It is currently being validated through an Amira Global project: P1196A.
We are investigating a ‘lab on wheels’, with the aim of making labs more flexible and mobile.
All these projects should prepare us for whatever is to come!
Contact information
Nucomat
Spieveldstraat 45
Ind.park E17/3265
9160 Lokeren
Belgium
Tel: +32 9 395 11 11
Web: www.nucomat.com
Email: info@nucomat.be
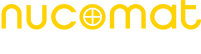