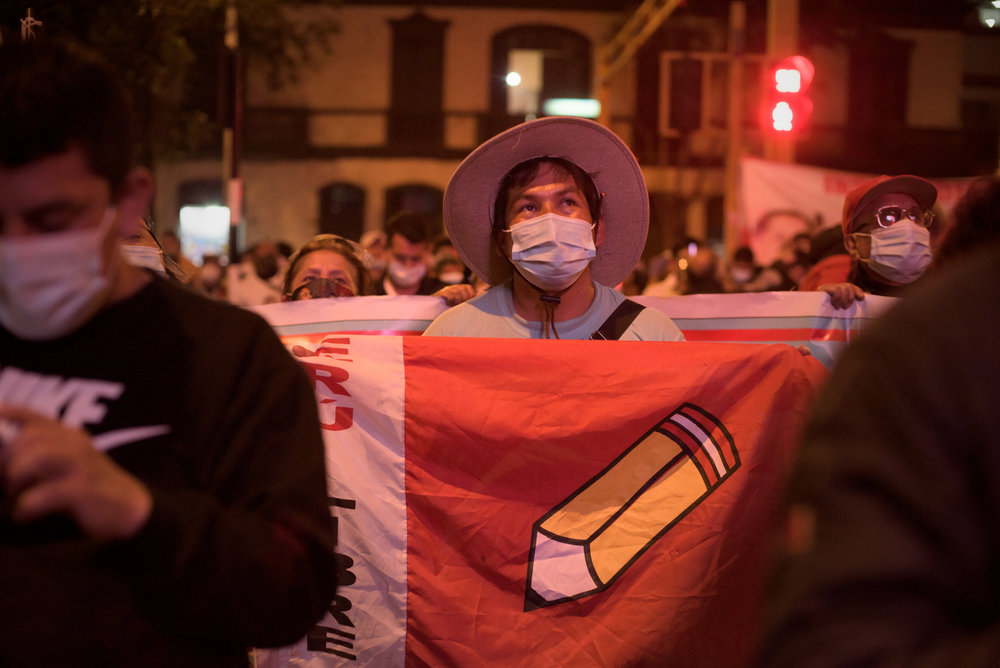
Policy
Mining under Castillo:
a threat or
an opportunity?
The election of Pedro Castillo to the position of president of Peru has led to fears that he will attempt a nationalisation of Peru’s vast minable resources. Zachary Skidmore explores what impact his appointment will have on the industry and how miners can respond to work with the new administration.
D
uring the early 2000s, Latin America experienced a populist reawakening, with a wave of charismatic socialist leaders coming to the fore in countries with some of the world’s richest mineral and energy deposits. What followed was a process of energy nationalism.
From 2002-2012, there were expropriations in Argentina, Bolivia, Ecuador, and Venezuela of private owned natural resources. Leaders including Hector Correia, Evo Morales, and Hugo Chavez nationalised their countries’ primary resource deposits to fund ambitious social policies.
The election of Pedro Castillo, a rural school teacher from the Marxist party, to the presidency of Peru has led to questions over whether he will follow a similar agenda and hold to his campaign promise to “recover sovereignty over all our natural resources”.
A mining giant
Peru is the world's second-largest copper producer, with large gold, silver, and zinc reserves. It has some $56bn of open mining investments, primarily in copper, and is home to mines owned by foreign companies including, Anglo American, Glencore, Southern Copper Corporation, and MMG.
Though Peru has benefited greatly from mining, many districts that should be prospering have not seen many investments. For instance, in 2014, the region of San Marcos made $50m in mining revenue, yet the area had no paved roads, hospital infrastructure, or water treatment facilities.
The impacts of Covid-19 have only exacerbated the industry’s divisiveness within Peruvian society.
Frequent mining protests have also put further pressure on the industry. In 2019, Peruvian president Martín Vizcarra authorised the army to maintain order at a critical mining port, a day before an expected new round of protests against Southern Copper Corp's $1.4bn proposed Tia Maria mine.
The impacts of Covid-19 have only exacerbated the industry’s divisiveness within Peruvian society. Peru has reported the world’s highest death toll per capita during the pandemic, which has also driven close to one-tenth of its population into poverty – fuelling widespread resentment amongst rural residents towards the mining industry.
Castillo's rise
Castillo experienced a meteoric rise to the presidential palace. His political campaign was permeated by attacks on the mining and resource industry, singled out for plundering Peruvian wealth.
He called for the nationalisation of gold, silver, uranium, copper, and lithium to "rescue" its strategic resources and redirect the mineral wealth away from rich mining companies to help alleviate widespread poverty. He also spoke of a desire to double the state's share of mining profits to 70% and use the funds to boost healthcare and education and reduce income inequality.
There are also people who are interested in contributing to support this government from all across the political spectrum.
Since ascending to power, Castillo has noticeably toned down his rhetoric, stating that he would like to form a pluralistic government: "We are structuring a work team, and I see there are also people who are interested in contributing to support this government from all across the political spectrum."
The appointment of Pedro Francke, a moderate leftwing economist, to finance minister has done much to assuage some of the fears that arose with Castillo’s election.
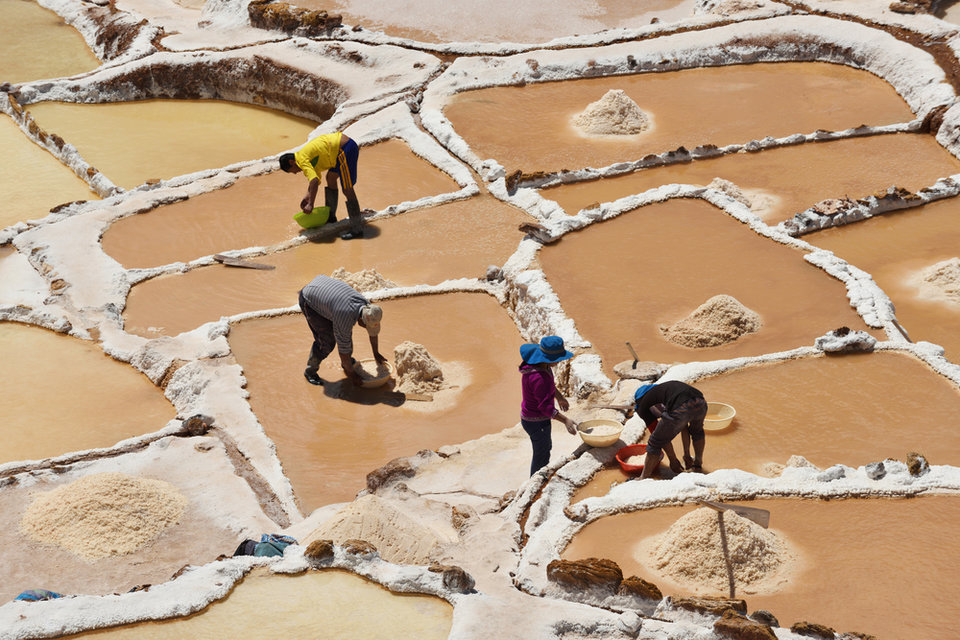
// Maras, Peru - September 03, 2016: Unidentified people at Salt evaporation ponds at the Maras salt mines at Maras, Peru, South America. Credit: astudio / Shutterstock.com
Social profitability
However, Castillo still intends to drive a more focused debate around the mining sector on taxation and its role in social programmes, especially within underdeveloped rural areas.
Central to this is the concept of social profitability. In his inauguration speech, Castillo stated that his administration would support private investment in mining and hydrocarbons if economically profitable and socially profitable for the surrounding communities to avoid conflicts.
This is supported by comments made by the new Energy and Mining Minister Ivan Merino. Merino said mines not only need to make money for private companies and generate tax revenue, but they should also support the population through improved infrastructure, respect for indigenous communities, and better environmental protection.
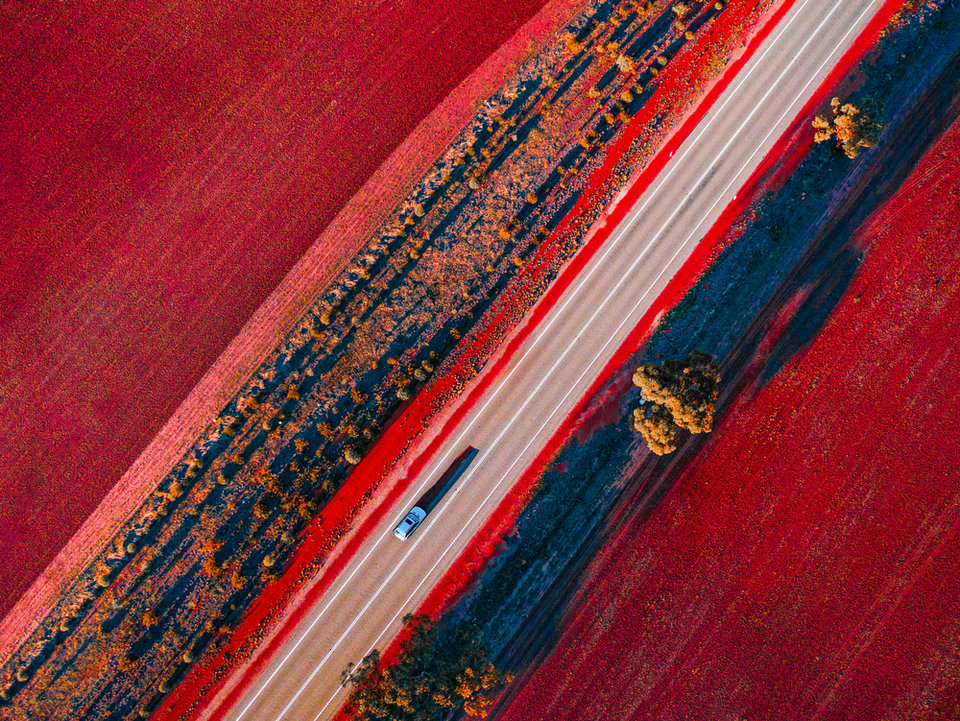
What this means for the mining industry
The initial reaction of the major mining interests within Peru has been muted. "This is the time for dialogue", the National Society of Mining, Oil and Energy, which represents leading industry companies, said in a statement.
There has been a concerted effort made by Castillo and Francke to engage with mining firms under the belief that prudent reviews of the tax rules will win them over. As Francke told Reuters: "In general, a good dialogue has been established, in which a significant part of the concerns they had have been eliminated, and I think there is a lot of openness,"
Mining interests in the country seem open to dialogue. Victor Gobitz, president of the Peruvian Institute of Mining Engineers, states: "If they (Castillo government) properly approach the subject and properly define the way to develop our country sustainably, we could create a perfect environment to develop our copper products. It is a matter of dialogue."
A significant barrier to this dialogue progressing, however, is the propensity in Peru for political uncertainty. Castillo came into power with a very narrow margin of victory. Perú Libre won 37 out of 130 seats in the legislative. The other eight parliamentary caucuses are all centre-right or right-wing, which will make most of his promises very difficult to uphold.
We must design and invest in the infrastructure which is cost-effective and is better for communities.
Despite the precarious nature of Castillo’s control, Victor Gorbitz argues that mining companies must continue contributing to projects of social profitability: “In order to properly develop our potential in terms of copper products, we must design and invest in the infrastructure which is cost-effective and is better for communities."
For the Peruvian mining sector to enjoy sustainable growth, community development must be central to its future strategy regardless of who holds the presidency.
However, despite the apparent positivity of talks, doubts remain in the industry. Higher taxes are "the main worry we have now”, said Pablo de la Flor, the head of the National Society of Mining, Oil and Energy, representing mining companies. Therefore, it is evident that the miners still hold a pessimistic attitude towards the new government, despite their openness to dialogue.
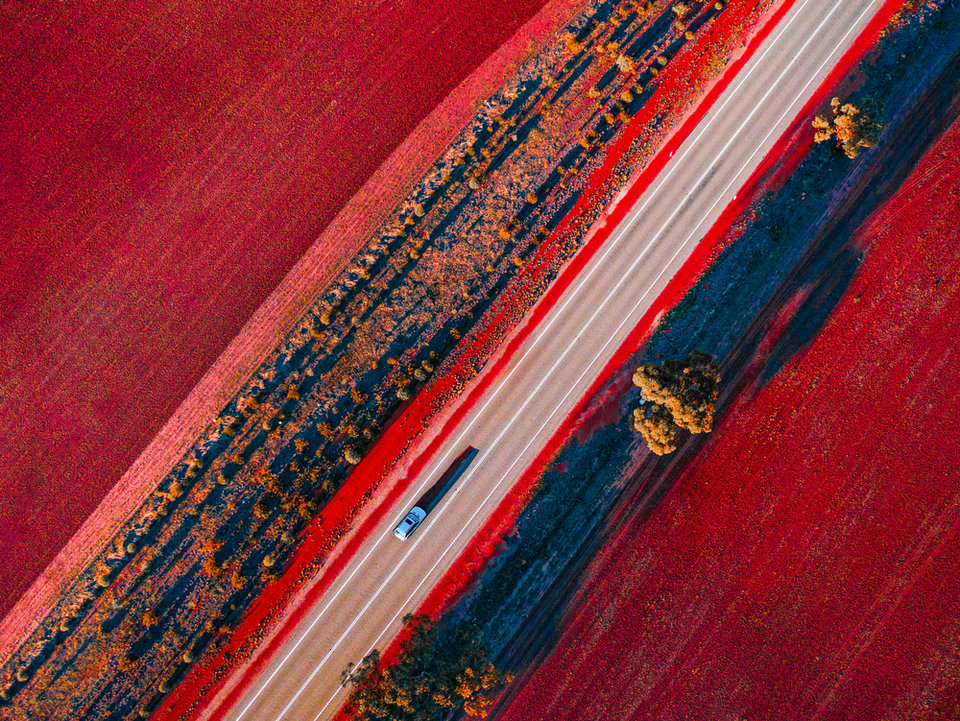
A brief presidency or lasting change
This has led some to envisage a lonely and potentially brief presidency, which could throw the mining sector already negatively impacted by Covid-19 into chaos, with political uncertainty and industrial action by mineworkers permeating the industry.
However, Castillo has already shown his effectiveness in resolving local conflicts between mine workers and miners in his intervention at the Las Bambas copper mine, which angry residents had blockaded for two weeks. Castillo wrote on Twitter that the protest standdown was evidence of how his government “was fulfilling its promise to find peaceful solutions to social conflicts”.
Therefore, it may be in the mining companies’ best interest for Castillo to experience a more stable presidency than his predecessors, as history has shown within Peru, that political instability will prove to negatively impact the sector’s financial and social profitability.
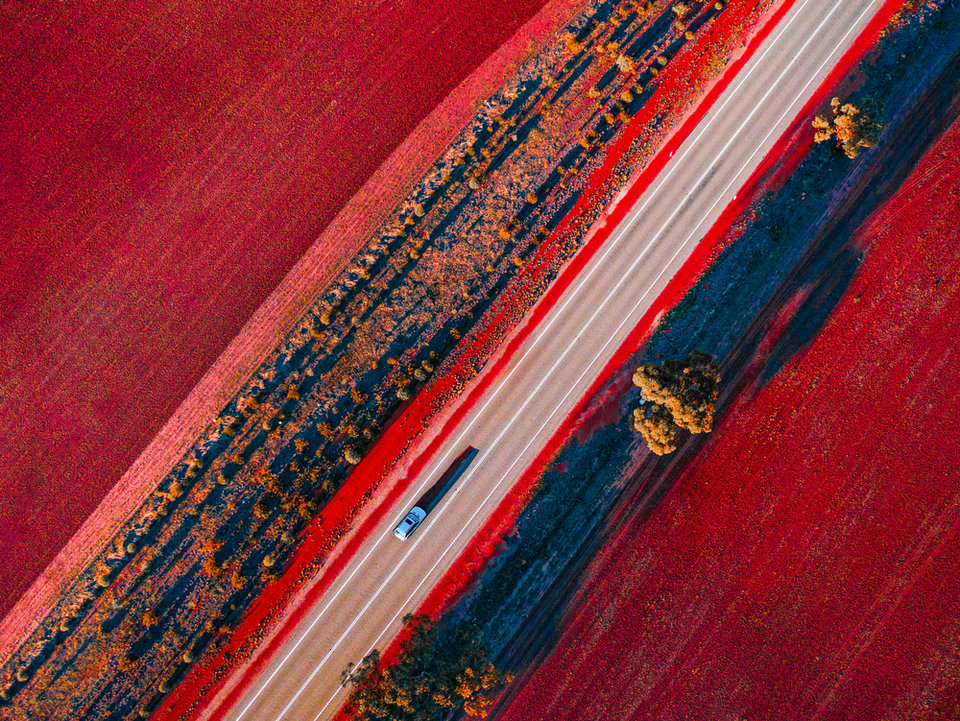
// Main image: Lima, Peru, June 09 ,2021: Supporters of candidate Pedro Castillo await the final result of the ONPE elections, in downtown Lima. Credit: Joel Salvador / Shutterstock.com