Company Insight
Sponsored by Mipac
Modern minerals
How Mipac is driving the shift from legacy to leading-edge tech.
Main image credit:
Since 1997, Mipac has grown from a small, ambitious team into a global powerhouse in mineral processing operational technology and control systems, known for solving the industry’s toughest challenges.
With over 720 successful projects under their belt, Mipac is empowering clients with best-practice automation and digital solutions, whether it’s building new operation, or modernising and optimising existing ones.
Steven Cohen recently spoke with Mine about Mipac’s strategic expansion into North America, the future of AI and machine learning in mining, and how Mipac is addressing key industry challenges like aging infrastructure and the skilled workforce shortage.
MINE Global: Steven, can you explain Mipac’s growth strategy in North America and what markets are a priority?
Steven Cohen: Mipac has been operating in the America’s for over a decade supporting clients from Alaska to Chile and points in between. We are strategically expanding our market presence in North America, particularly focusing on base metals, precious metals and critical minerals. This region is crucial due to its significant mining activity and potential for growth as the world transitions to a renewable power-driven economy. Our strategy involves leveraging Mipac’s global expertise in mineral processing, process methods and technologies.
We're bringing these proven solutions closer to our North American clients by establishing a local office in Tucson. This allows us to provide personalised support, which is essential in catering to the specific needs of U.S.-based mining operations. Furthermore, our existing relationships with major players like Anglo American, Teck Resources, Freeport-McMoRan, and Rio Tinto give us a solid foundation to build upon in this market.
By combining our global experience with a local presence, we’re positioning ourselves as a leading provider of mining solutions in North America, particularly as the industry navigates towards supply chain security, renewable energy and other future-focused initiatives.
MINE Global: How does Mipac’s approach to process automation and operational technology address the challenges faced by mineral processing plants in North America?
Steven Cohen: Our approach is designed to align perfectly with the specific challenges faced by North American mineral processing plants. We understand that the shortage of skilled labour, declining ore grades, rising energy costs, stringent environmental regulations, and aging infrastructure are major concerns.
Mipac addresses these through process optimisation, tailored automation solutions, and our deep expertise in systems integration. For instance, we help plants modernise by integrating new technologies with existing systems, thereby improving efficiency and reducing operational costs. Additionally, our vendor-agnostic approach ensures that we select the best technologies suited for each plant, regardless of their existing setup.
In short, Mipac’s comprehensive solutions help plants navigate these challenges effectively, improving their overall performance and sustainability.
MINE Global: We often hear about gaps in process automation and OT when it comes to meeting daily production targets. Can you elaborate on this gap?
Steven Cohen: Absolutely. The gap between current process automation and operational technology (OT) practices and the latest industry standards is evident in several areas. Many plants are still relying on legacy systems that are outdated and inefficient, which makes it difficult to optimise processes or respond quickly to changing conditions. Data quality is another critical issue; incomplete or siloed data hampers the effectiveness of automation systems and prevents a holistic view of operations.
Moreover, there's a noticeable skill shortage in the industry. Plants often struggle to find and retain personnel with the necessary expertise to implement and maintain advanced systems. This is compounded by the initial costs and uncertainties surrounding the return on investment (ROI) for new automation projects.
Addressing these gaps requires a strategic approach involving technology upgrades, improved data management, and workforce development. By doing so, plants can enhance their efficiency, reduce costs, and improve overall production performance.
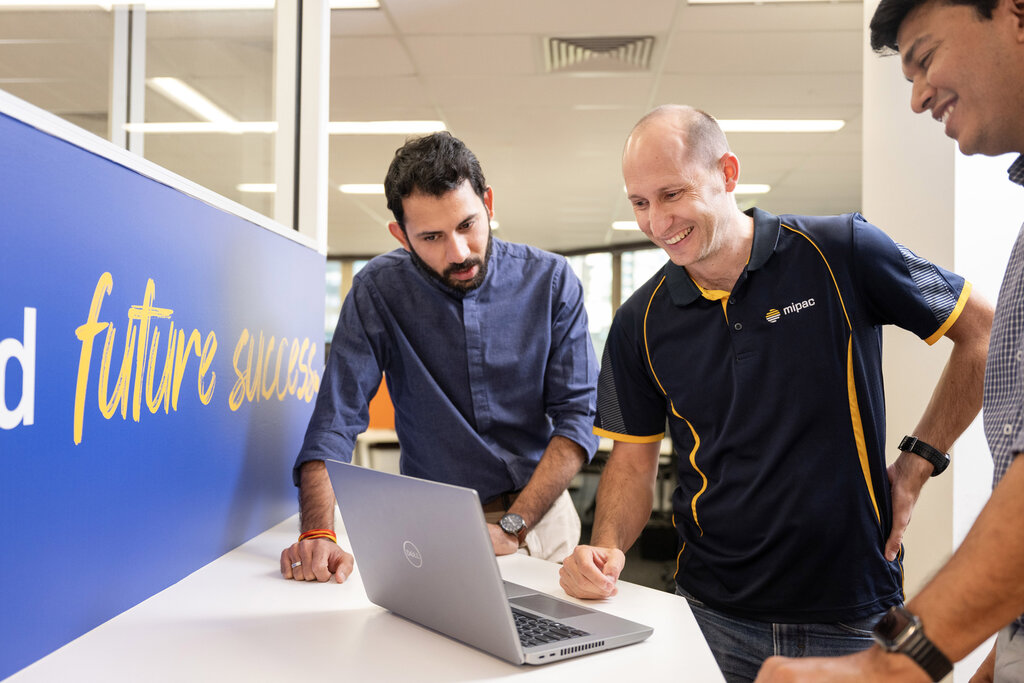
Caption. Credit:
MINE Global: With pressures such as aging infrastructure, outdated technology, and a skilled workforce shortage, how can Mipac assist companies in stabilising production?
Steven Cohen: Mipac is well-equipped to help companies stabilise their production amidst these challenges. We start by conducting thorough assessments to identify outdated or inefficient equipment. From there, we recommend and implement modern technologies that improve performance and energy efficiency. Our solutions also include automation and digitalisation to reduce manual labor and enhance process accuracy.
Moreover, we focus on workforce development through tailored e-training programs that upskill the existing workforce and attract new talent. We also provide remote support and troubleshooting to address technical issues promptly. Additionally, our predictive maintenance strategies use data analytics to foresee equipment failures and schedule proactive maintenance, thereby minimising downtime.
By addressing these critical areas, Mipac helps mineral processing plants stabilise production, reduce downtime, and meet their production targets efficiently. People play a vital role in the success of technology projects, and we prioritise incorporating change leadership to drive our projects towards success.
MINE Global: Operational efficiency is a hot topic in mineral processing right now. How is Mipac helping shape the future production of processing plants?
Steven Cohen: Operational efficiency is indeed crucial, and Mipac is at the forefront of driving this in mineral processing plants. We implement advanced process control systems that continuously optimise process parameters using real-time data. Predictive analytics play a significant role in our approach, allowing us to anticipate issues and proactively adjust operations to minimise downtime.
We also offer data-driven decision-making platforms that provide valuable insights into operational data, helping operators optimise processes effectively. Additionally, we are keen on workforce development, ensuring that employees are well-equipped to handle modern technologies, which is vital for maintaining continuous plant operation.
These strategies collectively help our clients achieve unprecedented levels of operational efficiency, improving both profitability and sustainability.

Caption. Credit:
MINE Global: What do you see as the biggest game-changer in operational technology for mineral processors in the next few years?
Steven Cohen: Artificial Intelligence (AI) and Machine Learning (ML) are set to be the biggest game-changers in the coming years. These technologies can revolutionise many aspects of mineral processing operations, from real-time process optimisation that maximises efficiency and minimises waste to predictive maintenance, which helps in reducing unplanned downtime and maintenance costs.
AI-powered systems also enable more precise grade control, leading to better mining and processing decisions. Furthermore, AI can facilitate autonomous operations in areas like mining and material handling, significantly improving operational efficiency.
However, the successful implementation of these technologies requires a robust digital foundation. Many mineral processors will need to embark on a significant digital transformation journey, upgrading their infrastructure and data management capabilities to fully unlock the potential of AI and ML.
At Mipac, we guide companies through this digital transformation, offering comprehensive services from digital maturity assessments to strategy development, and implementation planning, ensuring that they are well-positioned to leverage AI and ML for future success.
If you’re focusing on modernisation, automation, and data-driven decision making, get in touch with Mipac today.
Contact information
Mipac
Steven Cohen
Global Sales and Marketing Manager
Email: steven.cohen@mipac.global
Web: www.mipac.global