Feature
Treading carefully: industry looks to improve sustainability of mining tyres
Mining’s off-the-road tyres usage has become the next frontier for an industry looking to boost its green credentials, writes Andrew Tunnicliffe.
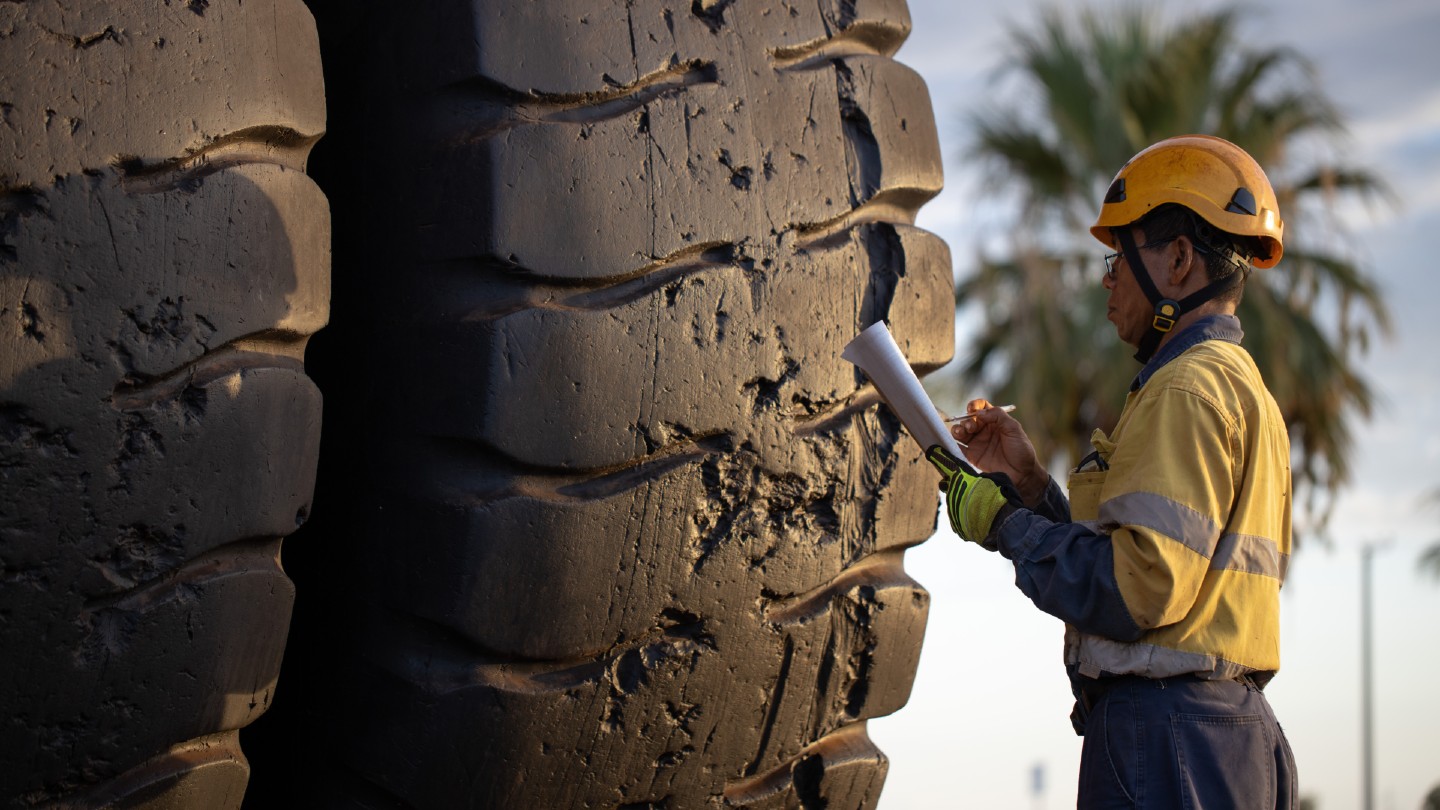
The mining industry is trying to improve sustainability by implementing strategies to better manage tyre life cycles. Credit: King Ropes Access / Shutterstock
From carrying enormously heavy loads to working in some of the toughest environments, often for extended hours, a lot is required of today’s mining machinery. Tyres, though, can sometimes go unnoticed.
Bursting with heavily researched compounds, designed with innovation at their core and manufactured at multimillion-dollar facilities, today’s off-the-road (OTR) tyres are the best ever made.
Although estimates vary, the global OTR tyres market is worth billions, and set to grow by billions more to the end of this decade. Despite this, the mining industry continues to face challenges when it comes to tyre life cycles and end-of-life disposal, which is frequently before its time.
Australia discards more than 130,000 tonnes (t) of tyres annually, while in Chile that figure is closer to 180,000t. In both countries, and around the world, what to do with tyres at the end of their life is a pressing issue, with mining companies increasingly looking for sustainability – but that surely starts with getting the most out of a tyre in the first instance.
Improving the longevity of mining tyres
Professor Angelica Vivanco and student Israel Mamami from Arturo Prat University in Chile say an estimated 90% of OTR tyres suffer premature failure. This, they add, is directly associated with the behaviour of companies that “prioritise productivity over tyre longevity”. It is of course a view mining would contest robustly, but it does have some merit – at least historically.
The wear of tyres depends on a variety of factors such as driver skills, weather conditions, equipment maintenance and road conditions.
The industry is, however, taking giant steps to counter premature tyre wastage. Mining companies are introducing strategies to better manage tyre life cycles and the supply chain is encouraging more mindful use supported by new maintenance technologies. Innovations in the materials and manufacturing processes used to make tyres more sustainable also show the sector is hungry for change.
However, the battle to be more sustainable starts with how tyres are used day-to-day. “The wear of tyres depends on a variety of factors such as driver skills, weather conditions, equipment maintenance and road conditions,” Vivanco and Mamami point out.
They highlight a case study at a mine in north Chile where 48 front end loader tyres and 223 mining truck tyres (with an estimated value of $5.1m) were discarded between 2019 and 2021. “Of these, between 80% and 90% were discarded prematurely due to operational damage, without reaching 100% of their service life,” they add.
AI supports tyre inspection
Supporting efforts to use mining tyres until they reach the 100% wear limit is an area where the supply chain can help.
“The greater the frequency and quality of tyre inspections, the more we can identify tyre issues early for longer tyre life, as well as more uptime,” explains Christian Erdelyi, manager of mining technology solutions at Kal Tire Mining Tire Group.
The Canadian-owned company offers an autonomous inspection and fleet maintenance planning package, TireSight, that addresses both the needs of increasingly autonomous mines and miners striving for greater safety, productivity and tyre performance.
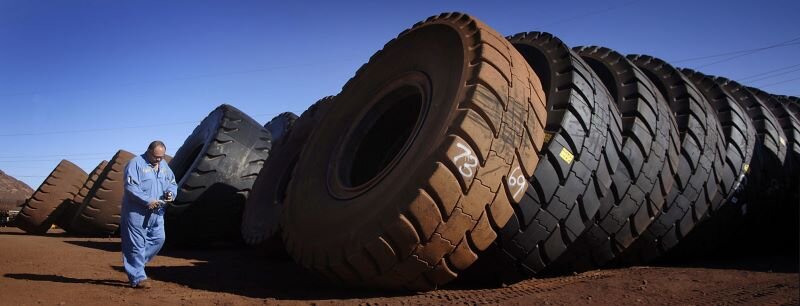
Tyres from heavy earth-moving trucks at the Tom Price iron ore mine in Pilbara, Western Australia. Credit: Jack Atley / Getty Images
Using Pitcrew AI’s autonomous tyre inspection offering, its own Tire & Operations Management System as the data hub and validation by expert condition monitoring teams, Kal Tire says it can increase the frequency and quality of inspections, reduce technicians’ exposure to trucks and ensure tyre work is performed accordingly.
Pitcrew AI is one of several technologies that uses AI to offer real-time continuous automated tyre inspections. It can identify issues known to compromise stability: heat, tyre separation, problems with braking systems and uneven loading. Placed at the side of a haul road, a solar-powered, pad-mounted unit uses thermal cameras to assess passing vehicles and warn of potential problems. It then shares vehicle ID, defect type and location and time data, with supporting images and video.
In a recent LinkedIn post, Pitcrew AI says it has conducted 670,000 inspections in the previous 12 months, helping to avoid at least 15 critical mine events worldwide. It adds: “Visual inspections might catch the obvious wear and tear, but they often miss the subtle signs that could lead to costly breakdowns.”
Haul roads: the route to improving performance?
Michelin also has haul roads in its sights. The company told attendees at MINExpo 2024 in Las Vegas on 24 September that it is bringing two “gamechangers” to market. These are the Michelin XDR4 Speed Energy™ Tire, with an optimised, more flexible tread and the “first energy-efficient” rubber compound designed to reduce fuel consumption and lower CO₂ emissions by running cooler, thus directing more energy towards the truck.
However, Michelin says haul roads are the backbone of any mine, impacting safety and driving productivity. “Keeping them maintained is often a manual, reactive process,” it adds. This is another area where technology could help.
Michelin Better Haul Road continuously monitors haul road conditions, providing analytics and data-driven insights to “help mines maintain safety and legal compliance, increase team efficiency and accountability, and prioritise resources and actions”.
The mobile and web-based software solution lets mining crews digitally capture and evaluate potential haul road issues, including the level of urgency, and share findings across teams with suggest next steps to take.
“This proactive approach… ensures that any issues are quickly resolved, minimising downtime and maintaining the flow of operations, while considering opportunities to reduce fuel and energy consumption,” says Christel Dubus, CMO for Michelin Mining Services. He adds that by monitoring haul road conditions the longevity and reliability of these crucial transportation routes can be ensured.
The need for enhanced haul road management is a position Vivanco and Mamami echo. “Maintaining clean and well-conditioned roads contributes to reducing [tyre] tread damage and avoiding load imbalances,” they state.
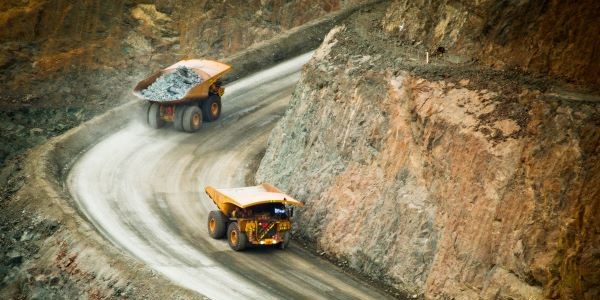
The condition of haul roads is key to maximising the life of OTR mining tyres. Credit: Jason Benz Bennee / Shutterstock
“Additionally, controlling tyre pressure is crucial for maximising tyre lifespan, which represents a significant opportunity to enhance both economic efficiency and environmental responsibility.”
Citing a separate case study, the researchers explain that between a half and almost three-quarters of tyres are discarded prematurely due to excessive tyre pressure.
Another study, published earlier this year Engineering and Applied Sciences by the University of Mines and Technology in Ghana, revealed the dangers posed to OTR tyres at mines.
Its authors wrote: “The predominant causes of significant tyre failures are multifaceted, including poor underfoot conditions, presence of water, operator negligence and incorrect tyre inflation. Other critical factors… are excessive heat generation, and mechanical stress such as spinning, skidding or sliding.”
Driving for a more sustainable tyre life cycle
With a growing knowledge base of what impacts tyre life cycles and how those can be blunted, the days of prematurely disposing of tyres may soon be something of the past. For some that could not come soon enough, with used tyres quite literally piling up at some mines.
Tyre manufacturers are responding to the calls for greater sustainability. Among its efforts Michelin has adopted metrics such as Life Cycle Assessment to evaluate the environmental impact of its products across their lifespan, and it is working to reduce them.
Meanwhile, Kal Tire’s Maple Programme aims to extend a tyre’s life through its re-tread and conventional repair offerings. “Demand is growing for sustainable supply chain solutions, and to be able to demonstrate those efforts,” says Miles Rigney, vice-president of Kal Tire’s Mining Tire Group Australian company. “Customers choosing our proven and environmentally friendly tyre solutions can show their stewardship and make a significant contribution toward a lower carbon future.”
When tyres truly do reach the end of life, even then they have purpose. For the past three years, Kal Tire has been turning them into alternative fuel, steel and carbon ash, and synthetic gas at a mine in Chile. Other uses have included BHP’s collaboration with authorities in Queensland, Australia, to resurface a major highway with crumb rubber. So, it seems that even when tyres come to the end of the road, in mining at least, there is still life left in them.