Feature
Can AI enhance mining's collision avoidance technology?
Andrew Tunnicliffe talks with SAPHI Engineering’s Liam Manning and Wabtec Digital Mine’s Mitch Tanzer about the impact of AI on collision avoidance systems used in the mining industry.
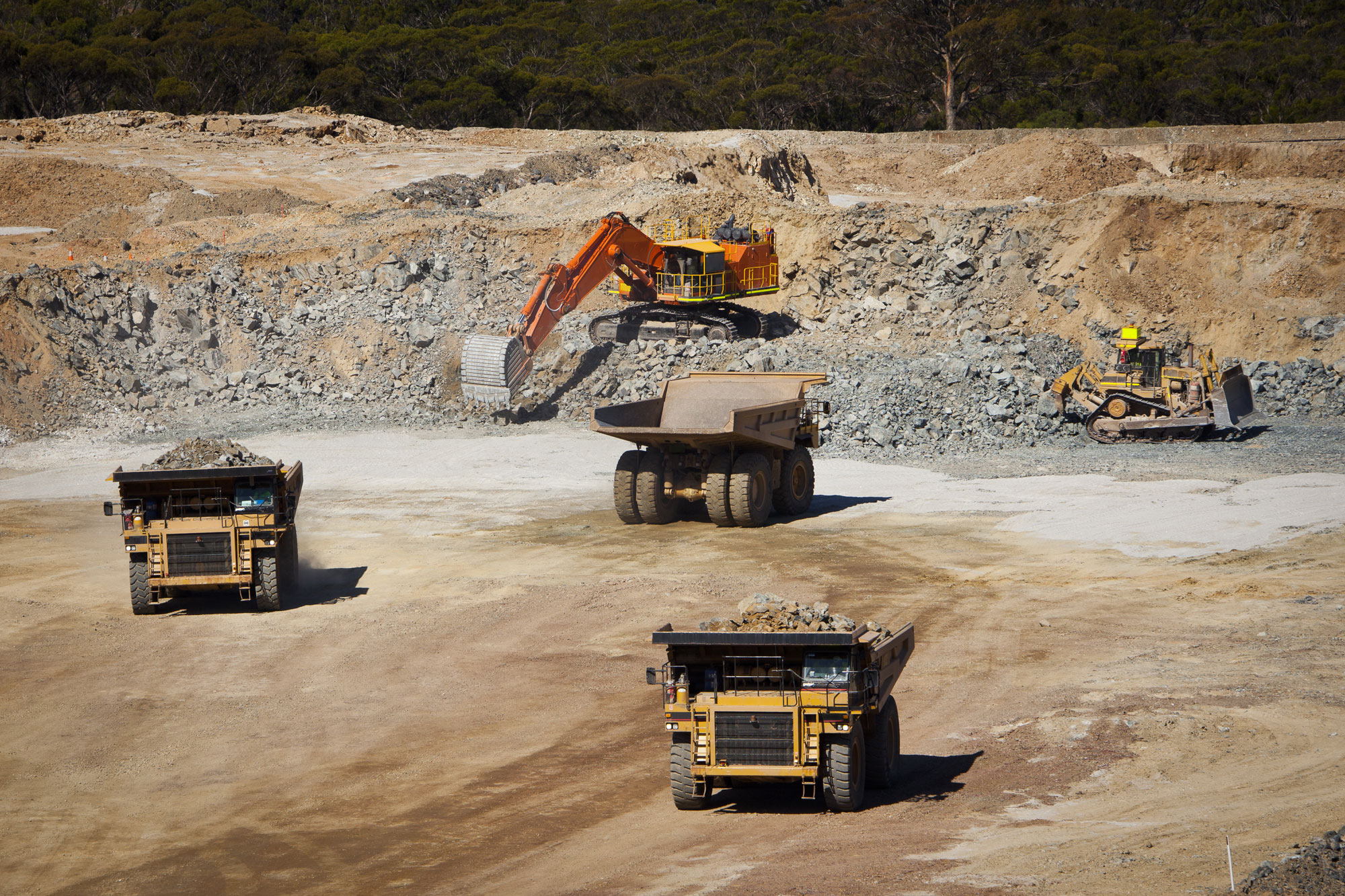
The shift from reactive detection to proactive collision avoidance technology could improve safety in the mining sector. Credit: Jason Benz Bennee / Shutterstock
Despite masses of research, copious statistical analyses and the endless logging of occupational data, it is still difficult to say exactly how many mine vehicle collisions occur globally each year. It is also hard to say how many people are injured or killed as a result.
In Australia, at least, the figures are comprehensively collected and made more widely available. Sadly, deaths from mining-related causes almost doubled in 2024 to 11, up from six the previous year, according to SafeWork Australia, an Australian statutory agency established in 2009. At least three of those involved vehicles.
Often the large amount of variables – from local geography to a region’s climate, the maturity of a site to the technologies used, and even the minerals and rare earths being extracted – make managing a mine a formidable task.
Add to that the possible fluctuation of the variables from hour to hour and shift to shift, and keeping workers safe is a unique mission at each mine.
Collision avoidance: dangers and mitigations
Among the challenges when trying to avoid collisions are limited visibility, poor communications and inadequate worker training and experience. Global commercial director at collision avoidance systems maker Wabtec Digital Mine, Mitch Tanzer, says changing road conditions, varying vehicle speeds and the presence of personnel on foot can complicate collision avoidance efforts further.
However, improved mine site infrastructure, from lighting to traffic management systems, enhanced training programmes and rigorous safety procedures are all good starting points. Technology, though, has become a key component too – and is likely to become more important.
Australia’s mines are home to an estimated 5,994 trucks, 1,956 dozers, 1,064 excavators, 868 motor graders, 747 wheel loaders and 47 electric rope shovels; collectively around 7% of the global fleet, according to GlobalData, as MINE reported last September.
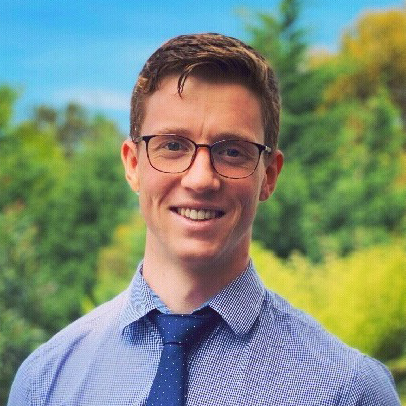
The last 5–15 years have seen significant advancements in collision avoidance.
Liam Manning, chief commercial officer at SAPHI Engineering
Here, sensors have become commonplace, as has radar technology and proximity warning systems. There is also a growing trend which, it is hoped, will help cut the risk of death or serious injury further – the adoption of remotely operated and autonomous vehicles.
Whilst these innovations have significantly improved safety, they still present challenges, according to SAPHI Engineering’s chief commercial officer Liam Manning. “The last 5–15 years have seen significant advancements in collision avoidance,” he says.
“Traditional systems relied on predefined detection parameters – whether through tags, GPS, LiDAR [light detection and ranging] or a related technology – delivering proximity alerts based on fixed rules,” he adds.
They, he explains, were built around fixed parameters and reactive alerts. Telematics-based solutions monitor vehicle locations and speeds, while smart tags and LiDAR detect proximity to nearby objects. However, he says that although these solutions are effective, they are not able to interpret complex environments or adapt to new risks without extensive manual reconfiguration.
“For example, a conventional system might trigger an alert whenever a vehicle was within a predefined distance of another object, regardless of whether it was an actual hazard or just a routine operation such as vehicles moving within designated zones,” he says.
Aside from what could arguably be false reporting, the bigger danger is they could lead to what Manning calls “alert fatigue”, resulting in workers ignoring or even disabling systems. The good news is that these technologies are always evolving and improving.
AI: changing the future of collision avoidance
However, there is a big change on the horizon according to Manning. AI is fundamentally disrupting how safety and operational monitoring works, introducing adaptability and intelligence not seen before.
“Instead of a system that just detects proximity, AI imaging technology, combined with existing proximity detection, offers a new level of flexibility,” he says.
The imaging and real-time data processing is a step beyond older systems, which only give operators a “limited and often rigid” view of potential hazards, Manning contends. Together they mark a fundamental change that is “redefining what is possible”, with a previously unattainable level of flexibility and intelligence.
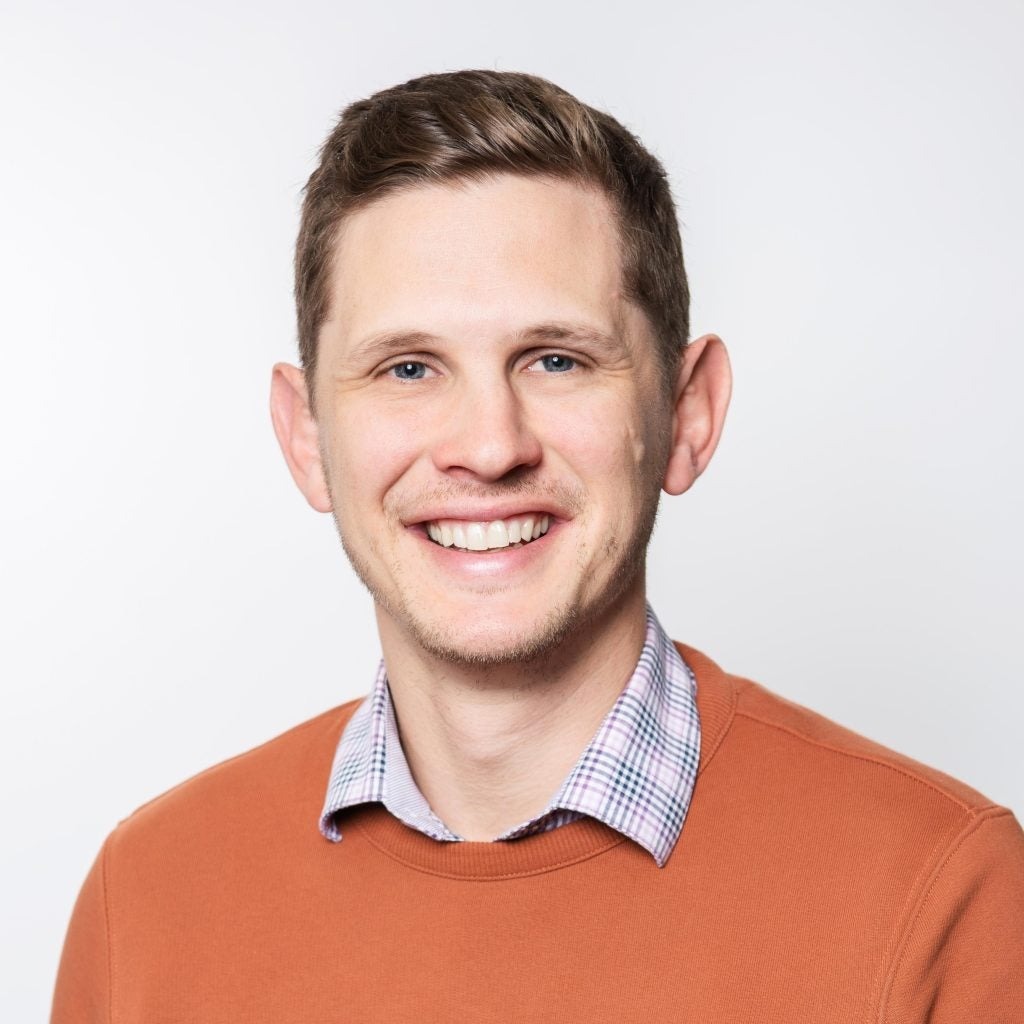
The use of AI in mining operations advances the technology to recognise more complex interactions in the dynamic environment of a mine site.
Mitch Tanzer, global commercial director, Wabtec Digital Mine. Credit: Wabtec
“Instead of just detecting objects, AI-powered imaging systems analyse context, distinguishing between a genuine risk and normal site activity. AI also allows for real-time decision-making,” he adds.
“The use of AI in mining operations advances the technology to recognise more complex interactions in the dynamic environment of a mine site,” says Tanzer. Their impact reaches further too; the systems learn and continuously adjust, improving accuracy and reducing false positives.
They can also be used across multiple applications, from collision detection and in-vehicle safety monitoring to increasing production efficiency, without adding new hardware or other infrastructure. Tanzer adds that the more data collected through AI, the more sophisticated the algorithms become.
Manning believes this shift from reactive detection to proactive intelligence will improve safety and efficiency by overseeing collision avoidance, driver monitoring and operational oversight in a single, consolidated adaptable platform.
“This means mining companies can deploy hardware once and evolve over time, rather than needing to replace hardware as their needs change,” he says.
Together, this would make collision avoidance part of a much larger ecosystem of intelligent, integrated solutions. It is a view Tanzer echoes, describing the potential for these systems to improve fleet management and performance, predict maintenance schedules and improve processes and workflows as “exciting”.
The dangers of fatigue
Increasing sophistication offers a wealth of analytical data to utilise, from providing context to risk detection and combatting warning fatigue, to on-site immediate responses, analysis for patterns of potential hazards, and the generation of comprehensive safety and efficiency reports, says Manning.
Speaking of worker fatigue, it is well recognised as a risk factor. Tanzer says this is another area AI collision avoidance systems can offer benefits in.
“Mining companies have done their best in terms of ‘lifestyle rosters’,” he says. “They now need technology to play a role. Monitoring fatigue levels ensures employees are operating at their best, improving overall mine productivity.
“As AI-driven models improve, mining companies can move beyond reactive safety measures and start using real-time, contextual decision-making to prevent incidents, optimise efficiency and improve compliance – all from a single, integrated system,” Manning adds.
The importance of training and regulation
However, while these advances could play a key role, they also introduce new risks and uncertainties, warns Manning. He says systems require continuous training, validation and oversight from experts to ensure accuracy. “I cannot emphasise this enough, there is a lot of smoke and mirrors out there,” he warns, urging potential procurers to see systems working in their environment before making any commitments.
This is a view echoed by Tanzer: “Whist the mining industry is good at implementing technology-based projects, collaborating with technology experts is fundamental to the success of both the overall project and AI system.”
Other concerns include regulations and standards…becoming stricter, potentially mandating real-time AI-based collision avoidance and fatigue monitoring.
He adds that installation should follow a structured approach that includes thorough scoping exercises, stakeholder engagement, change management, and training programmes for operators and maintenance crews, “all of which are critical success factors”.
Other concerns include regulations and standards – which Manning believes are currently not keeping pace with technological advances in this realm – becoming stricter, potentially mandating real-time AI-based collision avoidance and fatigue monitoring.
“Companies investing [must] stay ahead of regulatory shifts to ensure compliance, while maintaining operational flexibility,” he urges.
There is also the possibility that the cost of these technologies – as they move beyond vehicle-to-vehicle monitoring – may increase, potentially becoming a prohibitive factor. The increasing push for mine automation might also lead to a shift in how AI is deployed. “Will AI safety be needed in the same way, or will it evolve into a broader AI-based site management system?” Manning muses.
Then there is the ever-present cybersecurity risk, which he feels particularly strongly about. “We urge all mining groups to ensure that their AI vendors are local, have full transparency around integration and data flows, and demonstrable evidence of delivering to other major mining groups,” he says.
Waiting for the AI revolution
All that said, the future for AI collision avoidance is encouraging, with the technology past the early adopter phase and no longer untested or experimental.
“AI will revolutionise mining safety, but exactly how that looks is dynamic,” Manning declares.
For now, he says mining companies should start discussing widespread integration, regulatory clarity and real-world reliability to understand how quickly and effectively it could become standard practice for them.
“The lessons from early deployments have refined the technology, reduced risks and proven its effectiveness,” he continues. “That is not to say it is all sunshine and rainbows; there are risks and new areas to explore, but it has made significant progress.”