Company Insight
Sponsored by Lubrication Engineering
Meet the grease keeping Australia’s critical machinery moving
Standfirst...
Main image credit:
Lubrication is the foundation of maintaining maximum performance in critical machinery. Lubrication Engineering is a leading lubrication reliability company, specialising in all aspects of lubrication management. Their expertise spans lubricant handling equipment, single-point lubricators, and automatic lubrication systems with hundreds of lubrication points. In addition, they design and manufacture bespoke automatic lubrication systems, hold the global leadership position in wire rope lubrication technology, and import specialty lubricants to meet the diverse needs of their customers.
At the heart of their success is Almatek® Mine & Quarry LE1233, a grease that has saved businesses millions by preventing costly equipment failures.
We sat down with Managing Director Rodney Fitzpatrick to talk about Almatek’s origin story, what makes this incredible product unique, and how it keeps heavy industry moving in every state of Australia.
Can you give us a bit of background on Almatek and how it’s become so ubiquitous in heavy industry?
The Almatek history is an interesting one. There was a need in construction and transport for a product that would reduce pin and bush failures. I was working at the time, back in the mid-1980s in Victoria, and I got called into the William Adams Caterpillar dealer - they had a problem with their cushion hitches in a 613C scraper. It’s a massive pin that holds the machine together, and back then they were about $50,000 each. We went and re-engineered one of our existing products to meet the requirements for this application. Because it's so tacky and waterproof, it doesn't wash out or pound out, so it basically stopped all the warranty failures. Almatek was born. From that point on, that Caterpillar dealer actually stocked and sold Almatek for about 30 years. Even though Caterpillar subsequently bought out their own lubricants, they would still stock Almatek and sell to their customers, because it was so good.
We branded it Truck and Farm Grease back then and sold it in bright pink tubes, and eventually it was sold in every roadhouse in Australia and known as the #1 truck grease. Now, the reseller in Tamworth here has three or four red tacky greases called truck and farm grease, so we've been copied by everyone. But, while they might look red and tacky like ours, none of them will stand up to the rat trap test when you put them through it.
Click to edit...
Is the fact that Almatek LE1233 doesn’t wash or pound out unique across the industries you work in?
Absolutely. I used to do a lot of demonstrations with customers. I would just tell them to put some into their universal joints in their truck driveline. I’d point out, with their previous grease, as soon as they drive it down the road, they would have a fan of grease all on the underside of the truck where it has just thrown out. I ensured them, with Almatek, it’ll stay in there. I had a customer in Victoria, in the sand mines, who had an excavator that dug the sand out of the dams - so the bucket was underwater. They would only get about an hour and a half before the pins would start squealing so loud that they had to stop the machine. When they put LE1233 in, they'd go a full 8-12 hours of working and not have to regrease the machine, even in the highly acidic water of the sand mine.
What kind of savings are we talking about for those who make the switch?
You get savings in a number of ways. We found that when you go to regrease with it, you basically put only a third of the amount back in, compared to other greases. Our largest customer, for example, uses about 15 tons a year, which is significantly less than they used to, so that adds up. The second saving is the extended intervals between greasing. Instead of greasing every day, a customer might do every two or three days.
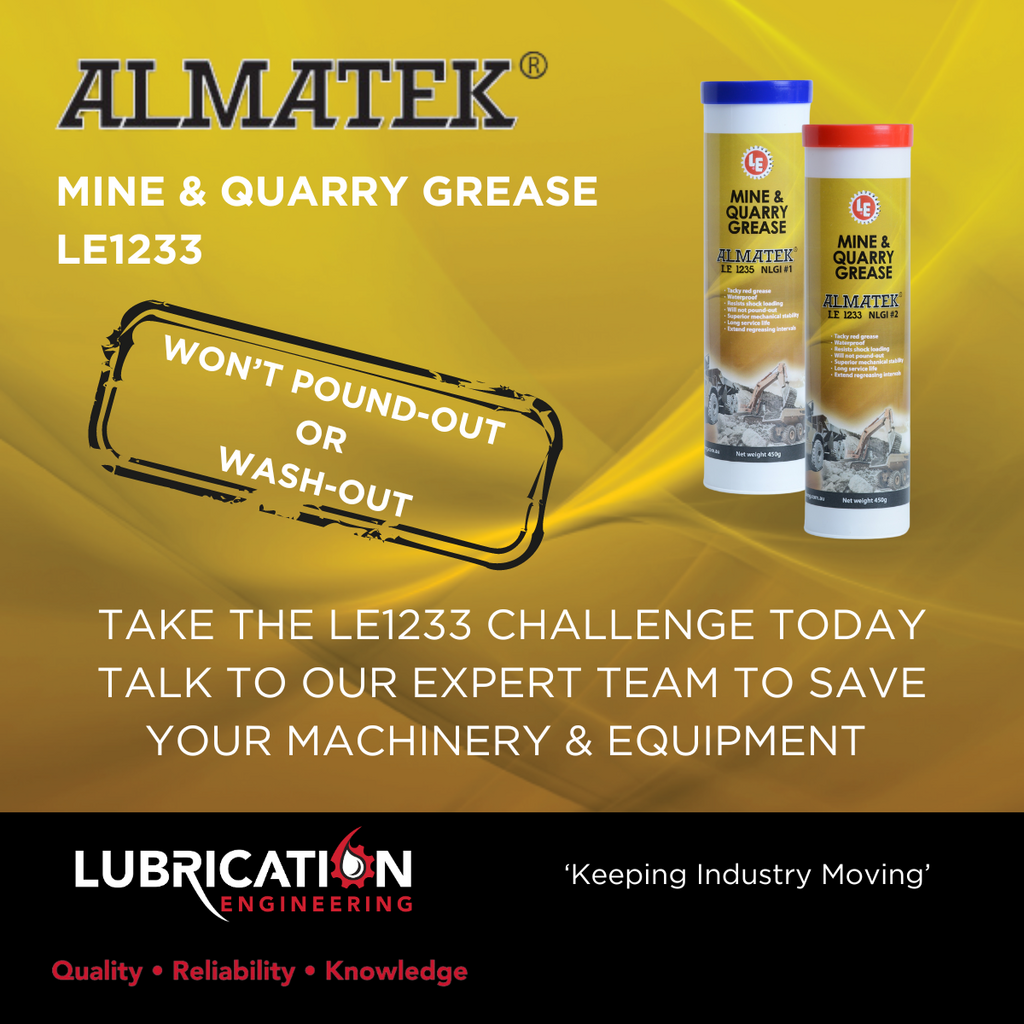
Caption:
But the biggest saving is the reduction in pin and bush wear. We've got a really good example of that. We did a trial with the second largest gold mine in Australia, up in the Northern Territory. After we did some training up on site, they brought up a problem they had with the pins and bushes in their underground drill rigs. Because they drill vertically into the roof to put bolts in, the water runs straight down the drill and into all the pins and bushes - they were having failures as often as every two weeks. They did a 12-week trial where they rebuilt their drill arms with new pins and bushes, put Almatek in one drill arm and their previous grease in the other, and after 12 weeks the arm with Almatek in it had one pin and bush failure, while the arm with grease from our competitor had 16 pin and bush failures in that 12-week period.
They started using it for their pins and bushes on all their drill rigs, and we went back to them a year later, they said they had saved $200,000 just in the cost of replacing the pins and bushes. Not machine downtime, not lost production, not on the reduced volume of grease, just on the pin and bush replacement.
Keep your machinery moving with Almatek® LE1233
Don’t let costly breakdowns slow you down. Almatek® Mine & Quarry LE1233 is the proven solution to extend equipment life, cut maintenance costs, and keep operations running smoothly. See the results for yourself!
Contact information
Lubrication Engineering
Unit 1D/201 Power Street,
Glendenning NSW 2761,
Australia
Tel.: +61 1800 676 699
Email: sales@lubeng.com.au
Web: www.lubeng.com.au