Company Insight
Sponsored by HNA Group
Under pressure
How two diesel fitters are taking the risk and re-designing tooling.
Main image credit:
Based in the Bowen Basin, HNA Group was born out of seeking a different way to conduct high risk work. HNA Group designs and develops purpose-built solutions like hydraulic tooling covers, elimination of live work tooling, custom made burst sleeve kits for machinery and now the all-new strut handling device, all aimed at making tasks safer and efficient. With a client base that includes industry giants like BHP, Rio Tinto, and Liebherr, HNA Group is making waves through innovative and practical engineering.
We spoke with Co-founders and Directors Anthony Lye and Craig Hall about how they came up with their innovative solutions for the mining industry.
Talk us through how HNA Group came about
Craig and I were working together on an excavator, and during a maintenance shut down we were going through the idea of how we can make just a couple of tasks safer for the rest of us while working with hydraulics and hydraulic tooling.
From this we decided to create our HNA Band Cover, HNA Hydraulic Tool Sock and Hydraulic Cylinder Covers - these were three very simple devices that we knew were going to help in reducing the risk of high-pressure fluid injection injuries.
From those three tools it was an evolution more than anything. We were diesel fitters on the tools, away from home working on various mine sites trying to create safer ways of conducting maintenance. For four years we juggled diesel fitting and getting HNA Group off the ground.
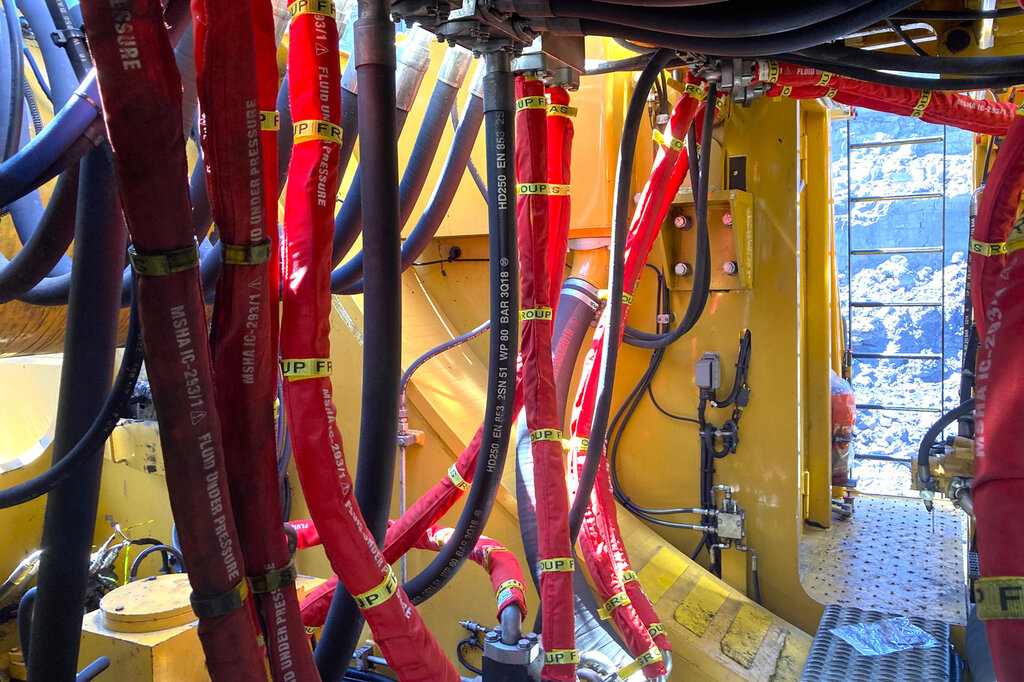
HNA Group Burst Sleeve Kit installed on a CAT 6040: The custom-engineered hydraulic protection kits are designed to safeguard critical circuits without unnecessary bulk coverage.
You mentioned conceptualising and developing products over time, what did that process look like, and how did your different products come about?
It started off addressing hydraulic fluid injection injuries and creating covers to reduce that risk. When you’re working with hydraulic tooling, the potential for a hydraulic pressure release is more common than you think. The hydraulic tools have a working pressure of around 5,000 to 9000 PSI, if a release of pressure occurs it can inject oil directly into your skin, which is called a high-pressure fluid injection injury. The results of this injury are devastating and leads to months of surgeries and possible loss of limb or life.
After we created our band, hydraulic bolting tool, and cylinder covers, we started manufacturing customised burst sleeving kits for machinery. Our burst sleeve kits are the first of their kind, we have taken the time to create a cost and maintenance effective way to cover hydraulic hoses. These custom kits are RS23 and MDG41compliant, they are manufactured to match high risk identified circuits, we currently have 200+ kits catalogued. Inside the kit, each sleeve is part numbered to match the OEM hose part number, the installation of the sleeves are very simple due part numbers and diagrams.
We have some pretty big clients using our burst sleeving: Liebherr Australia, BHP, Rio Tinto, Thiess, Mackellar, and Coxons Group, for example.
From there, we expanded into elimination of live work tooling. BHP conducted a campaign called Project Tutus, through this we designed, developed, and manufactured elimination of live work tooling. These items were then implemented throughout their Queensland mine sites.
From the Tutus initiative, the maintenance redesign team from BHP tasked us with the redesigning and upgrading one of their existing strut handling tools.
The existing tool previously did not meet the mine site engineering requirements, so we re-engineered the tool to Australian Standards and replaced the original controls with a safer, battery-over-hydraulic (24-volt) system, we also upgraded the strut rotation from mechanical drive to hydraulics, and introduced a remote control.
Click to edit...
Our Strut Handling Tool is now a safer and more efficient way to change out front strut assemblies on CAT haul trucks suiting models 777, 785, 789, and 793.
With this tool, we have eliminated the process of dual lifts, complex lift plans and uncontrolled movement.
We currently have three of these tools in circulation and the feedback has been extremely positive from safety officers and managers. They have commented saying that the change out process has now been streamlined and saving around six hours per changeout.
It looks like you guys are really starting to make a difference in the mining sector, I am quite interested in the Strut Handling Tool that you upgraded, can you explain a bit more about it?
We started with an existing tool, which we found a few flaws in, so it needed refining for the end user. We worked with BHP a lot through this, and we spent time seeing the old tool in use and talking with the fitters about what they would like to add or change.
We worked out that we could add a push bar, we then incorporated that push bar to allow an area to house the electrics, batteries, and the remote-control receiver, then decided to upgrade the rotation of the strut by removing the old mechanical worm drive and replacing it with a hydraulic cylinder.
After our testing was complete, it was time to bring it all together, we ensured that all components were engineered and certified, added extras such as guarding, tie down points, and signage.
Once the tool was made, a transport frame was incorporated into the builds. This frame carries the extra adapter plates and incorporates a solar panel with isolators to charge the batteries on the strut tool.
What's in the pipeline in terms of expansion and product development?
Our products have already organically grown throughout the mining community due to our high-quality custom and practical solutions. And no doubt word of mouth will continue to keep us growing in the Australian market.
As for product development, we do have a few tools that we are going to convert from both air driven and three-phase power down to our 24VDC battery-over-hydraulic technology. So, watch this space….
Contact information
HNA Group Pty Ltd
Anthony Lye
Tel.: +61 041 244 6807
Email: anthony@hnagroup.com.au
Craig Hall
Tel.: +61 040 937 7930
Email: craig@hnagroup.com.au
Web: www.hnagroup.com.au