COMPANY INSIGHT
Sponsored by: ANDRITZ Separation
Enhanced efficiency in tailings treatment with intelligent process control
ANDRITZ Separation provides mechanical and thermal technologies, services and automation solutions for the chemical, environmental, food, mining and minerals industries
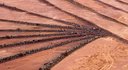
T
ailings are an ever-present problem on the global mining market. A case study in Brazil shows the potential of filter presses with the latest control system becoming a gamechanger in handling this issue.
Located in the municipality of Sarzedo, Minas Gerais, Brazilian company Itaminas has been producing and processing iron ore since 1959. Due to their activities being carried out and guided with business acumen and an environmental and social conscience, they are one of the first mining companies in Brazil to decommission tailings dams associated with the production of iron ore concentrate.
Looking for an alternative to dispose of its tailings, the company decided on the implementation of a filtering system and subsequent stacking of dry tailings, and on ANDRITZ Separation as their partner in this task. With the title “Eliminating tailings dams through a sustainable solution”, this project applying ANDRITZ filter press technology for the elimination of tailings dams, with its positive impact on the environment and the community, even ended up winning the PMI award for the best project of the year, organized by the PMI® Santa Catarina Chapter, in late 2021.
With the 24th Mining Metallurgic Industry Minérios Magazine Excellence Award under the title “Stackable, safe and sustainable: smart approach to tailings”, a second award followed shortly afterwards.
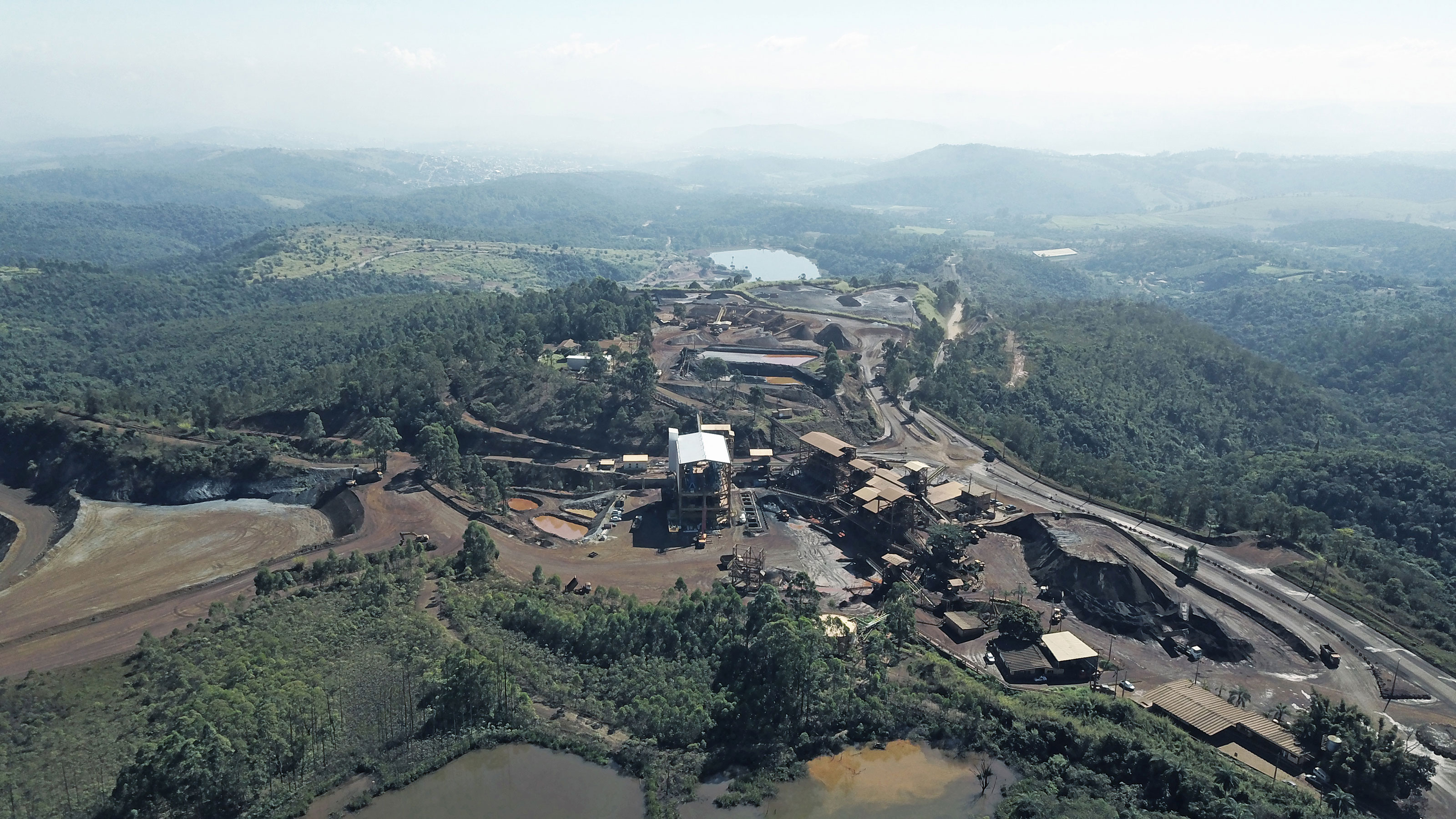
Itaminas iron ore plant in Minas Gerais, Brazil (© ANDRITZ, Itaminas)
Subheader
After tests showed that a membrane pressurization system with water would be the best way of achieving the geotechnical moisture content in the cake required for dry disposal and in order to secure a high throughput, four ANDRITZ overhead filter presses in the largest size of 2500 x 2500 mm were chosen as the ideal equipment. All water filtered out of the tailings slurry is reused in the iron ore processing plant, while the remaining solids are discharged to tailings stockpiles. The recovery of clean water from the filtration process is currently estimated at approximately 80% or 2,200 m³ per filter press, avoiding plant outages during the dry season and reducing the need for fresh water from springs, lagoons and wells. With a consistently achieved moisture content of around 17% and a cake density of 2.5 t/m3 in performance tests, the final performance delivered was 34% higher than expected.
To tailor the presses to the specific needs of Itaminas, they have bilateral feed connections, for example the iron-ore slurry is fed into the machine from two sides – the front and the rear – while the filtrate is discharged through eight outlets. The presses also have a second feed port and a mixed package of membrane and rigid chamber plates that can be easily accessed from the side. However, the real stand-out feature of the filter presses is their automation system, which allows for excellent results in the operation's performance to be achieved. The equipment operates with mechanical availability between 95% and 98%, working 22 hours a day.
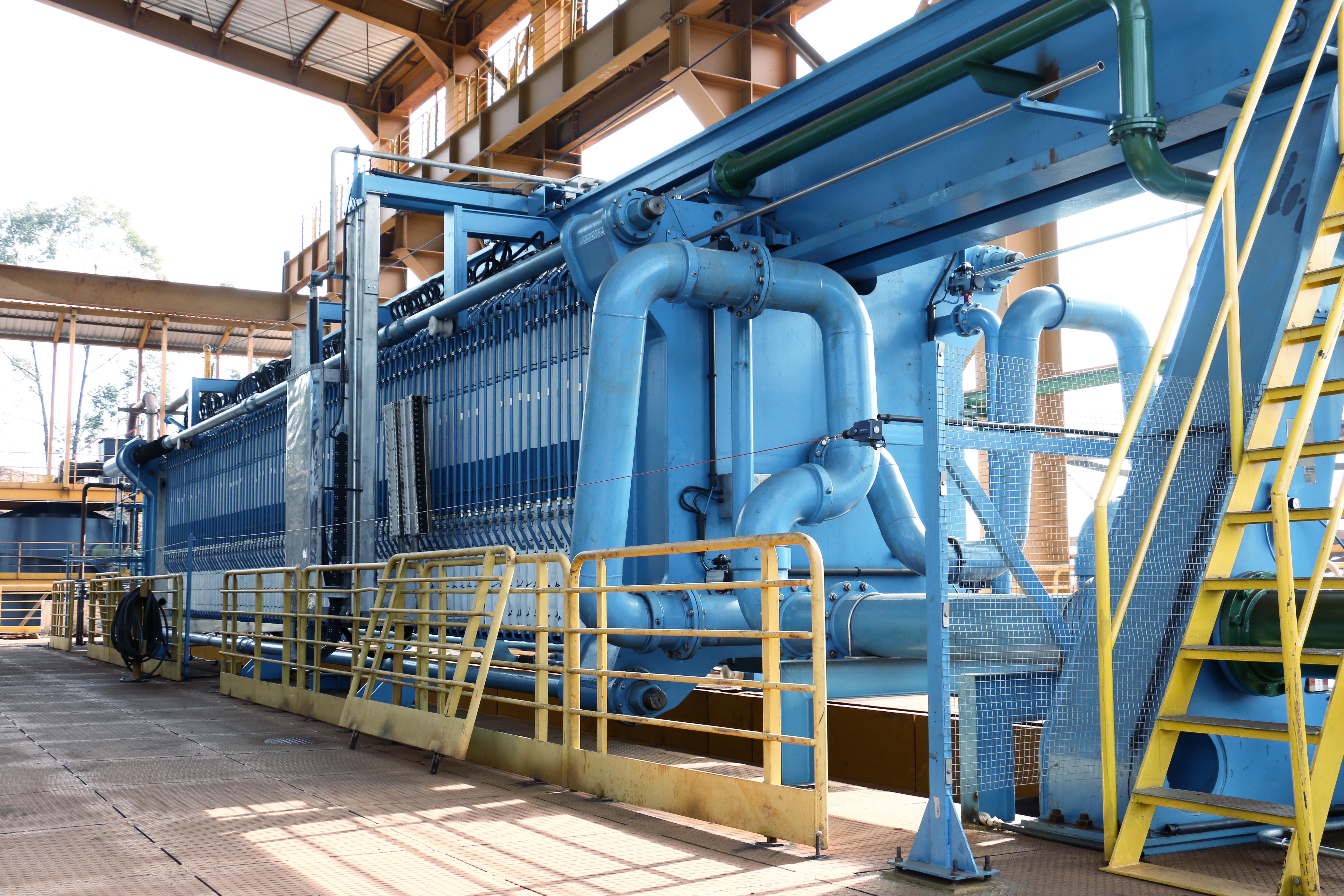
ANDRITZ overhead filter presses A4 F 2500 with a future-proof control and automation system for tailings treatment (© IMAGINE IMAGENS INCRÍVEIS)
How intelligent filtration equipment is cutting the costs of tailings treatment
As tailings treatment is not a process step that turns a profit, it should be handled as cost-efficiently as possible. In the case of Itaminas, this is achieved by equipping the filter presses with a Metris addIQ Prime control system. Metris addIQ control systems are part of Metris, the ANDRITZ brand for digital solutions, and are one of the most innovative automation solutions on the market today.
The control system chosen by Itaminas combines state-of-the-art hardware with high-end trending and diagnostic functions, maximizing the performance of the filter presses. With a 12’’ panel touchscreen as standard, its design allows intuitive operation, crossing barriers of language or training. Combined with Metris addIQ Connect, it provides the resources for remote monitoring in the future, also enabling remote support for fast interaction between the on-site machine and the ANDRITZ specialists.
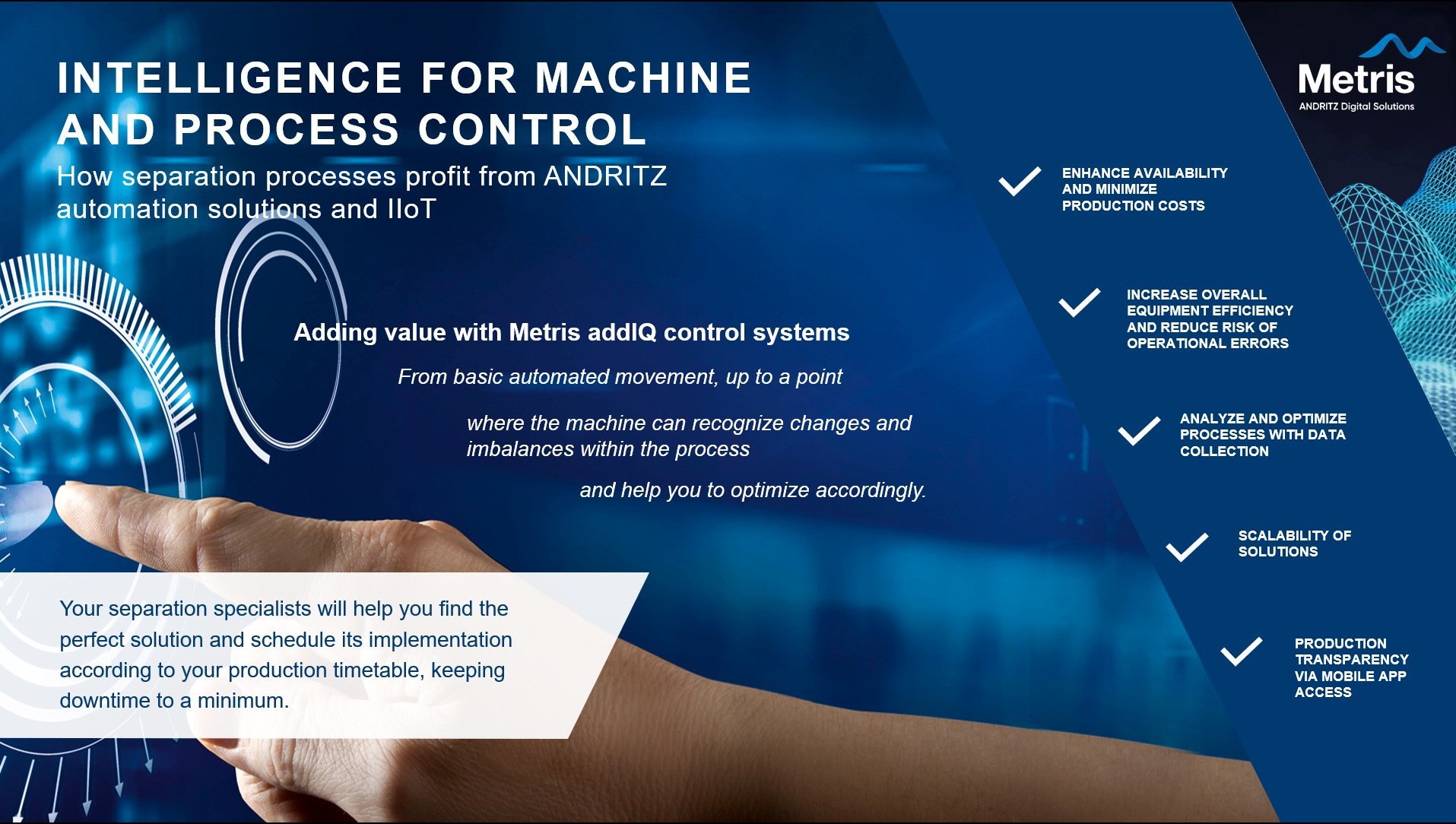
Metris addIQ Connect enables use of the filter press app for Windows, Android, and iOS (smartphones, tablets, and PCs), one of the most interesting features for the tailings treatment process. With this app, the operator is able to directly access process live data as well as machine-related documentation. Furthermore, the control system collects and stores the performance data of the filter press for later analysis, be this to further improve performance or to enable predictive maintenance. Different KPIs are shown in one step on the filter press radar screen, giving a quick overview when any intervention is needed.
Combined with an automatic e-mail notifier for the most critical process alarms, the operator can take action immediately if values differ from the norm. Additionally, automatic reports are generated (every shift, every day, every month) that include process values and the corresponding trend curves, and these can also be forwarded to an e-mail recipient.
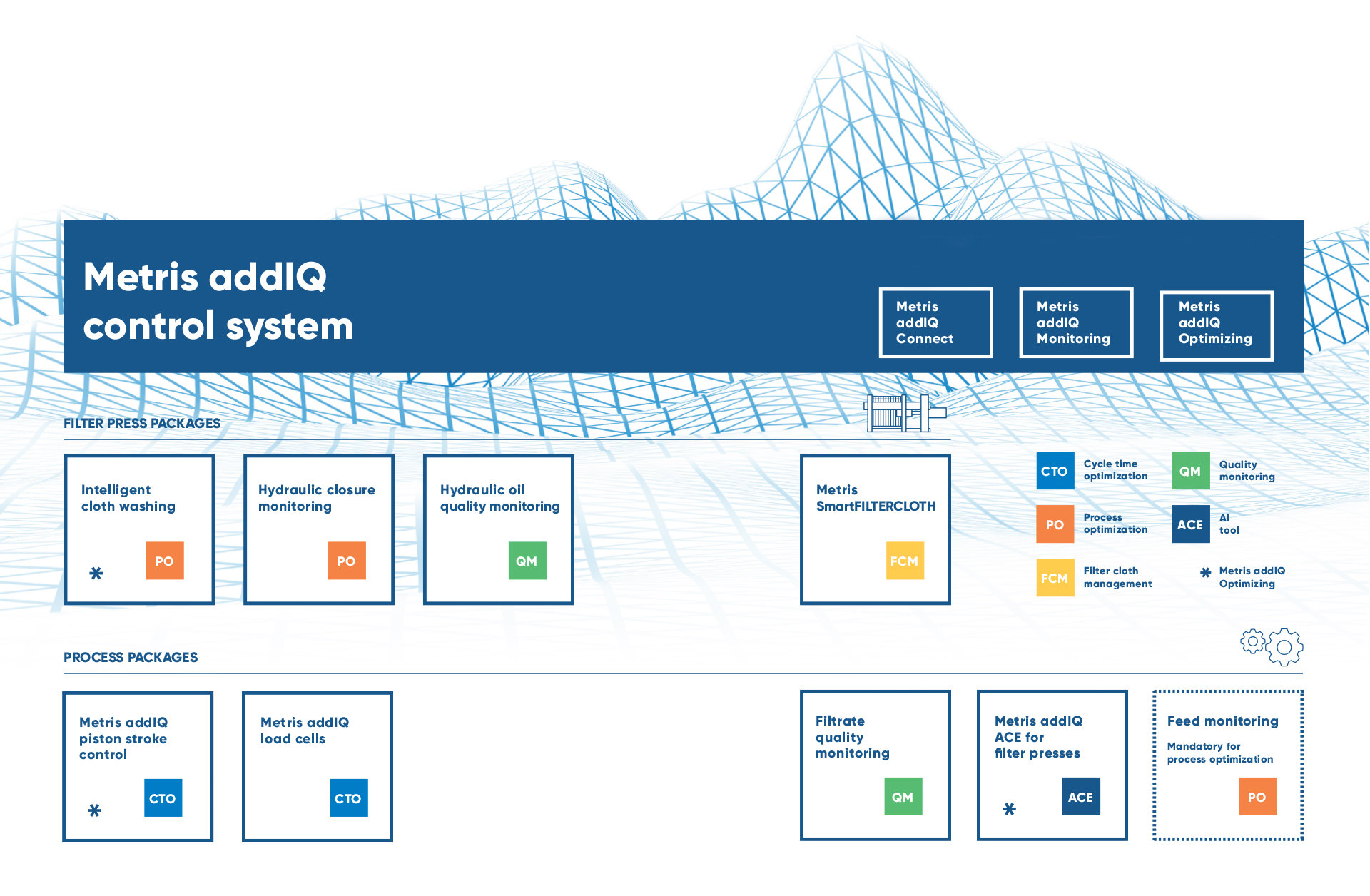
Overview of all packages and features included in ANDRITZ’s Intelligent Filter Press
Intelligent filter presses go one step further, including even more beneficial features: Consistent automated monitoring of the shifting plate angle is another advantage of intelligent filter presses. When small amounts of cake remain on the plates, they become more and more misaligned after every discharge – intelligent sensors are able to detect the angle changes and inform the operator when the ideal time would be to start a washing cycle, making the machine less operator-reliant. Another standout feature that is simple, yet clever, is the plate package divider. This detail enables a noteworthy increase in the speed of cake discharge, providing discharge times as short as 0.5-1 second per plate and, therefore, increasing capacity.
Small features like this are what enables the intelligent filter press to raise tailings dewatering to a new level and take a huge leap towards potentially autonomous machine operation in the future.
Why LaseTVM-Line
EXPERIENCE
30 years of experience in laser measurement technology for volumetric measurements in mining, steel, bulk material logistics, ports etc.
RELIABILITY
Reproducible, non-manipulable measurements, exclusion of the human error factor.
ACCURACY
Exact determination of volume, excludes inaccuracies due to material moisture.