Company Insight
Sponsored by MATO Group
Technology in motion
How MATO leads the way in belt maintenance and lubrication equipment.
Main image credit:
Established in 1906 in Offenbach/Germany near Frankfurt, MATO has been a pioneer in the mining industry, originally focusing on coal mining operations. Over the years, the company has diversified its offerings to become a leading provider of belt maintenance and lubrication products servicing a wide range of industries. From light to heavy-duty applications, MATO's solutions encompass belt maintenance, cleaning systems, conveyor belt components and lubrication equipment, serving virtually every sector where conveyor systems, belts and lubricants are utilized.
With worldwide subsidiaries and strong present in Europe, MATO is a key supplier of Belt Maintenance Equipment and Lubrication Equipment throughout his network.
At MATO, ensuring uncompromising quality is paramount. Our products are integral to safety-related applications, especially in environments like underground mines where conveyor systems play a critical role in transporting personnel and materials. Our rigorous quality assurance protocols, spanning the entire supply chain to product dispatch, adhere to a zero-error principle. Every employee at MATO shares the responsibility for maintaining these high standards, with suppliers seamlessly integrated into our quality management system.
Belt maintenance equipment
MATO stands at the forefront of mechanical conveyor belt splicing technology, offering a comprehensive range of belt maintenance equipment. Designed to work seamlessly with MATO fasteners, our belt cleaning systems complete the product suite. Applications for these products span diverse industries, including mining, agriculture, recycling, airports, and the food and textile sectors.
MATO fasteners are engineered to withstand demanding operational conditions, providing operators in coal mines and processing plants with the assurance of safely moving thousands of loads daily. The synergy between fasteners and cleaners is critical to the effective, safe, and economical functioning of conveyor belts. MATO belt cleaners excel in delivering efficient cleaning performance, extended service life, and easy maintenance, enhancing the overall performance of conveyor systems.
Primary and secondary belt cleaners
Installation of primary and secondary belt cleaners plays a pivotal role in optimizing conveyor system performance.
Primary belt cleaners, available in tungsten carbide for vulcanized conveyor systems and polyurethane for systems with mechanical fasteners, effectively remove bulk material flow from the conveyor, reducing carry-back material and minimizing spillage.
Secondary belt cleaners, also offered in tungsten carbide variants, are positioned behind the head pulley to tackle sticky, fine, or wet materials that primary cleaners may not address. Multiple secondary cleaners can be installed for extreme applications, ensuring thorough cleaning and mitigating the risk of belt mis-tracking and component wear.
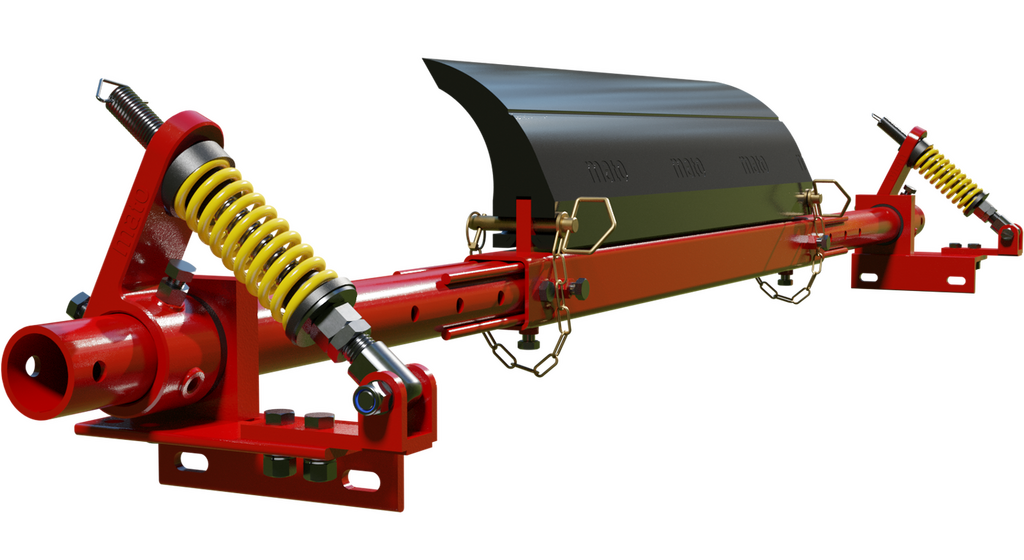
Caption. Credit:
Lubrication equipment
Every machine or piece of plant has moving parts. Lubricants are necessary to reduce friction, minimize wear and to offer protection against the intrusion of impurities and corrosion. These lubricants can only fulfil their defined and intended functions if they are delivered cleanly, safely and in the required volumes.
In all sectors of production, maintenance and repair, lubricant is often delivered at high pressure creating risks for operators, machinery and the environment. The complete range of MATO lubrication equipment enables our customers to handle and supply lubricants reliably, safely, economically and ecologically.
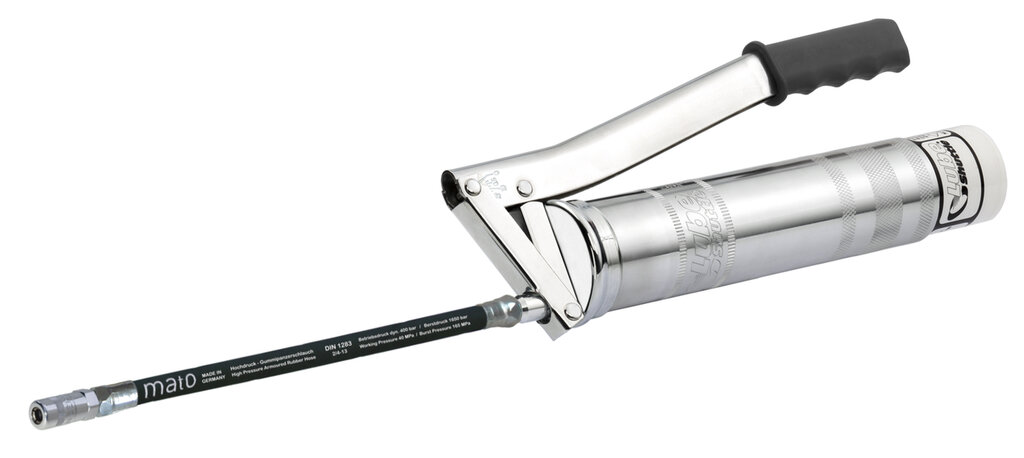
Caption. Credit:
Contact information
MATO GmbH & Co. KG
Benzstraße 16-24
63165 Mühlheim am Main
Tel.: +49 (0)6108 906 0
Fax: +49 (0)6108 906 120
Email: mato.germany@mato.de
Web: www.mato.de