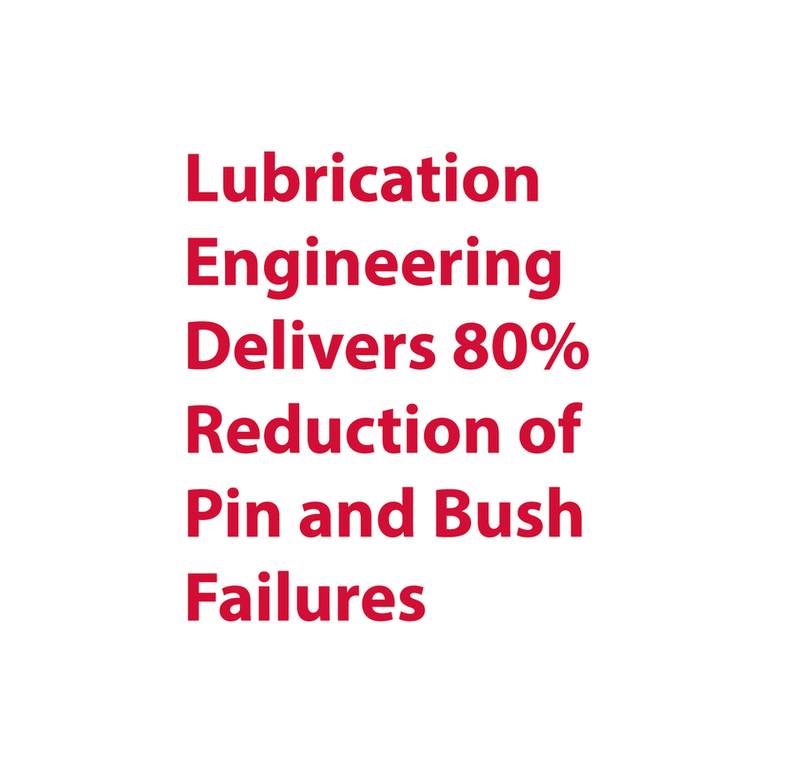
CHALLENGE
Short life-span of pins and bushes
SOLUTION
Almatek® General Purpose Lubricant (1233)
RESULTS
• Reduced pin & bush failures from 16 per quarter to just two
• Achieved annual savings of AUD 200,000 in cost of spare parts alone
Customer Testimonial
A Gold Mine, Northern Territory, Australia
Customer Profile
A large global mining company operating an underground gold mine in the Northern Territory of Australia.
Application
Underground Sandvik® jumbos, cable bolters and production solos.
Scroll down
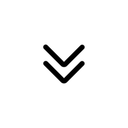
Challenge
The typical life span of most pins and bushes in the underground equipment was very short – just two to three weeks. Due to the high operational demands of the mine, greasing intervals for the more than 40 pins and bushes on each machine were often missed. The operation of each machine caused high vibration and a pounding action within the joint. Each joint was also subjected to high volumes of water during operation, which caused conventional grease to wash away. By the time maintenance teams were finally able to grease the joints, it was common to find them dry – with no grease at all lubricating the pins and bushes. This resulted in high rates of wear and corrosion, causing the joints to lose operational tolerance and even seize completely.
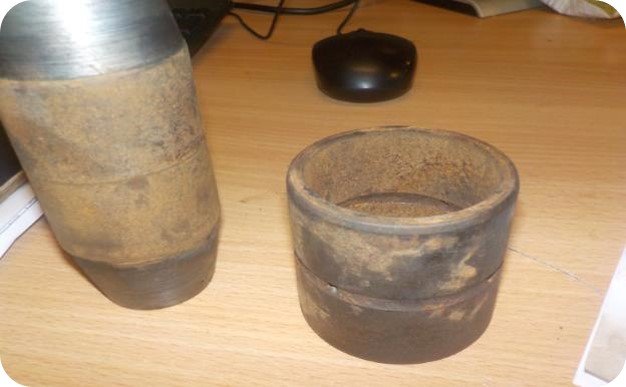
Typical Pin and Bush premature wear and tear
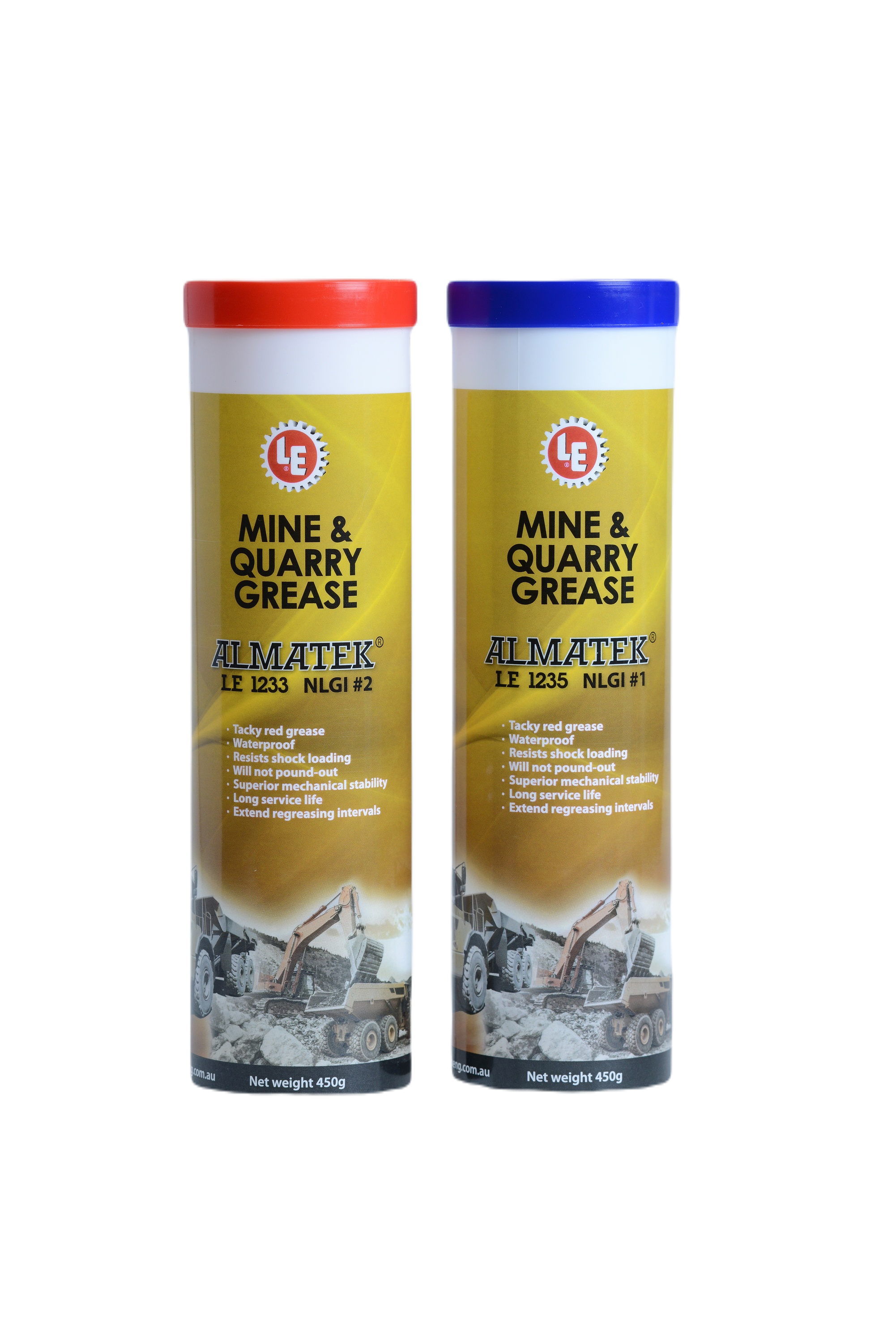
Lubrication Engineering Solution
The competitor grease previously used and recommended was a heavy duty NLGI 2 grease. Lubrication Engineering Australia recommended Almatek General Purpose Lubricant (1233) for the application due to its ability to withstand high shockloading and pound-out, as well as being 100% waterproof. Almatek 1233 contains two of Lubrication Engineer’s proprietary additives, Almasol and Quinplex.
RESULTS
Trials were conducted using two machines; one operating the existing competitive grease and the other using Almatek 1233. Operational hours and wear rates were monitored, and failures recorded for each. During the 12-week trial, the machine using the existing competitive grease had a total of 16 pins and bushes replaced whilst the machine using Almatek 1233 grease replaced only two pins and bushes. Following these results, savings were calculated at more than AUD 200,000 per year in parts alone for the fleet. The mine subsequently changed over to Almatek General Purpose Lubricant for all their underground mobile equipment.
The company has now extended trials to the surface fleet and into another of its larger mines located in Western Australia, with comparable results expected.
The ‘Rat Trap Video’ demonstrates the excellent ability of the Almatek General Purpose Lubricant (1233) to withstand pound-out and shock-loading.
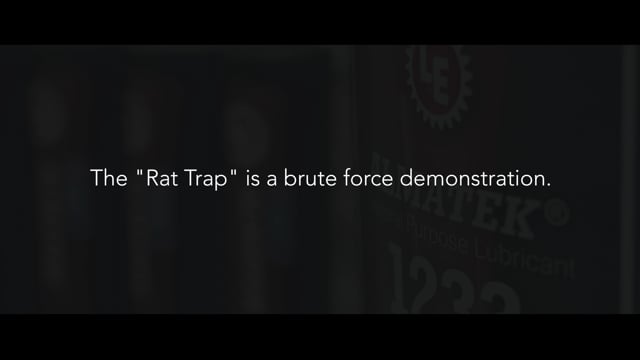
Company Profile
Lubrication Engineering are leaders in providing integrated lubrication maintenance solutions. Our expert team provides the best advice and products when it comes to high-quality oils and greases, contamination, and lubrication storage systems along with lubrication transfer systems.