COMPANY INSIGHT
Sponsored by Matec Pacific
The industrial excellence in italian machinery, by nature
Appreciation of the effect of changing regulations enables mine operators to proactively assess and respond to their relative exposure. A proactive response enables the operator to retain control of change processes in advance of a regulatory direction enforcing the change, the resource demand and the timeframe.
By way of example, Aspect Environmental looks at the requirements of the NSW Mining Amendment (Standard Conditions of Mining Leases – Rehabilitation) Regulation 2020 and how operators can respond and retain process control.
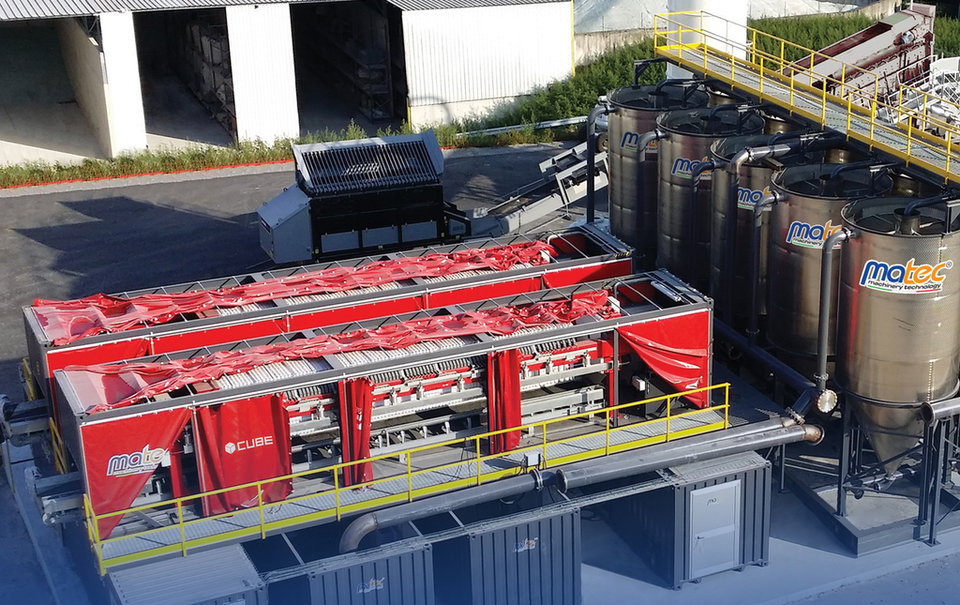
Visualizing the size of the world’s mine tailings
Tailings are what is left over after economic mineral are separated from mined rock. They comprise ground rock material and liquid waste from mineral processing plants.
They are mine particles mixed with water, forming a slurry that is stored in ponds or dams. The volume of tailings and their storage pose a risk to the natural and human environment.
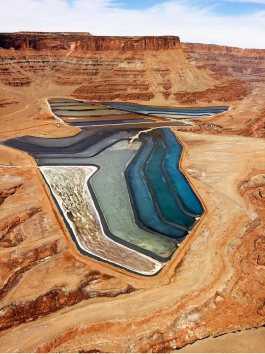
Global tailings
The Global Tailings Review estimates that the total number active, inactive and closed storage facilitiesis 8.500 with 217km3 of tailings, enough to fill a cube 6km high.
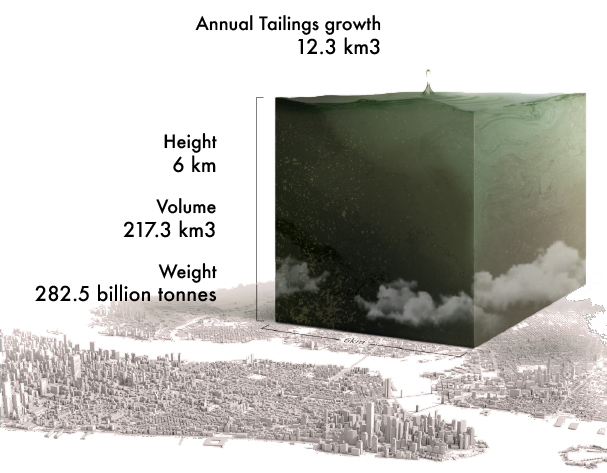
Contribution to global tailing, bycommodity

Some metal produce more tailings than others. The type, quality, quantity and production decisions of mineral deposits determine the amount of tailing waste as specific mine produces.
Visualizing the size of minetailings
On January 25th, 2019, a10-meter tall wave traveling 120km/h, washed 10million m3 of mining waste from the Brumadinho tailings dam over the Brazilian countryside killing some where between 270 and 320 people. This was a man made disaster, made from mining the materials we use daily. Every copper wire in your house, steel frame in an EV, or any modern appliance comes from mining.
Mining leaves behind waste in the form of tailings stored in dams or ponds around the world. This infographic takes a look at the estimated size of one part of this waste, tailings, visualized next to the skyline of New York City as a benchmark.
What are tailings?
Not all rock that comes out of the ground is metal. Miners find, remove, and refine rocks that carry a small amount of metal we need .72billion tonnes of material produced just over 10 billion tonnes of ore. Only 14% mined material makes it to processing for metals.
Tailings are what is left over after mills separate the metal from the mined rock. The processed material “tailings” comes from the “tail” end of a mining mill and comprise fine particles mixed with water forming a slurry. Mining companies will store this waste in dams or ponds.

The volume of waste material produced per unit of commodity is increasing due to declining ore grade. Tailings are only going to grow as population grow and grades decline.
What we offer
Cut costs and risk with smarter water and tailings management
As water becomes more expensive and difficult to source, recover and transport, the business requirements for responsible use of water are becoming increasingly important.
About 70 percent of mines operated by the major mining companies are located in countries where water stress is considered a major risk.
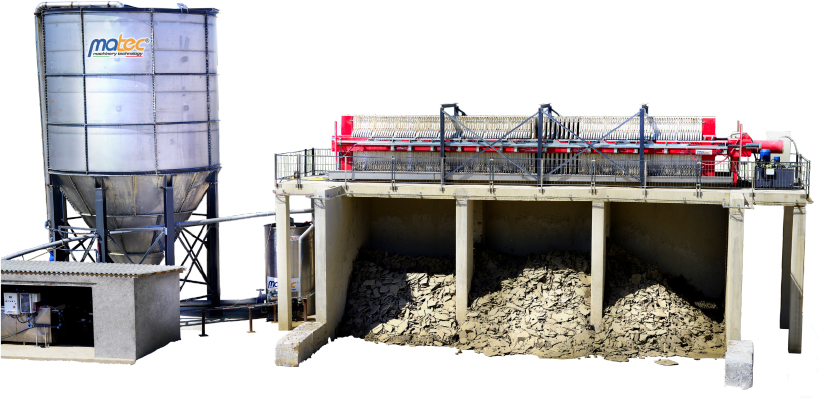
Case study
The oldest iron mining operation in Brazil, Casa de Pedra holds more than 6 billion tons of resources and 3 billion tons in reserves.
The ore is mined in four bodies and is sent to processing in the Central Plant (wet route) or the Mobile Plants (dry route), located near extraction areas.
Casa de Pedra currently has a production capacity of 30 million tons per year. Products resulting from the beneficiation process are grain, sinter feed and pellet feed.
The ore is transported to the Port of Itaguaí (TECAR) via rail terminals located in Casa de Pedra and the Pires Complex.
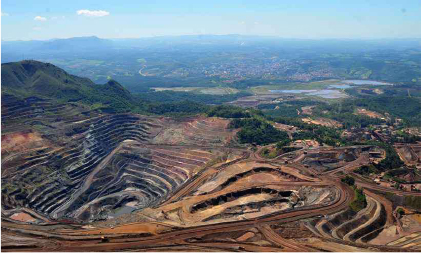
Case study
Deciding to decommission its upstream tailings dam, CSN went in to design and construction of its new MATEC dry stacking plant in the early parts of 2018, breaking the complete installation into 2 stages.
Stage1: comprising of 2x Vertical “HighRate” Thickeners and 4xMagnum 2000/190 PLTTT2 Fast Filter Presses fed straight fromCSN’s tailings dam and was successfully commissioned towards the end of 2018.
Stage2: plans to eliminate the feed to the upstream tailings dam entirely whilst still rehabilitating the tailings dam. The plant comprises of 3xVertical “HighRate” Thickeners and 5xMagnum 2000/19 0PLTTT2 Fast Filter Presses
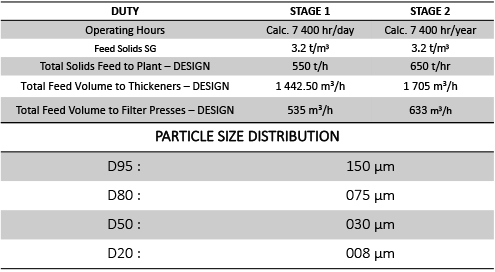
Case study
CSN phase one plant design
Installed Power (kw): 1 182
Plant Foot Print (LxW): 62m x 15m
Plant Volume (LxWxH): 18 600m³
Installed Compressed Air Rec.: 4 x 2m³
FILTER PRESS MODEL: MAGNUM2000X2000
NUMBER OF PLATES: 190
NUMBER OF UNITS: 4
OUTPUT OPTIONS:Conveyor discharge – Cake removed with conveyors and stock piled by a radial conveyor
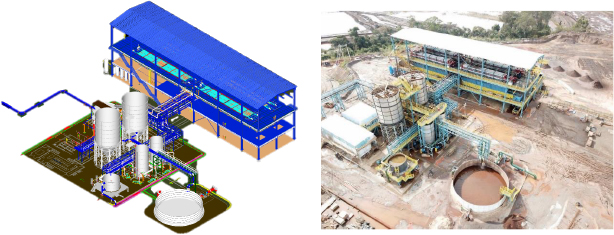
Case study
DESIGN: 550 Tonnes per Hour
ACTUAL: 585 Tonnes per Hour
(AVG. 4.4 Mt per Annum)
< 15%Residual Moisture
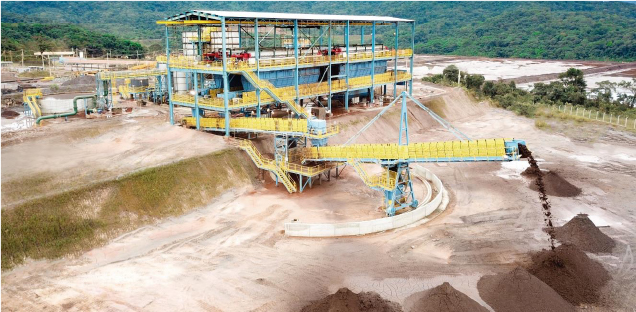
Contact information
Matec Pacific
Tel: +61 449 864 719
Web: www.matecpacific.com
Email: info@matecpacific.com