REMOVAL OF TOTAL SUSPENDED SOLIDS AND TURBIDITY:
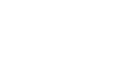
The DMI-65® particle size distribution is engineered to provide a perfect filtration coefficient resulting in excellent mechanical filtration lowering total suspended solids (TSS) to less than 1mg/L and turbidity levels less than 1 NTU.
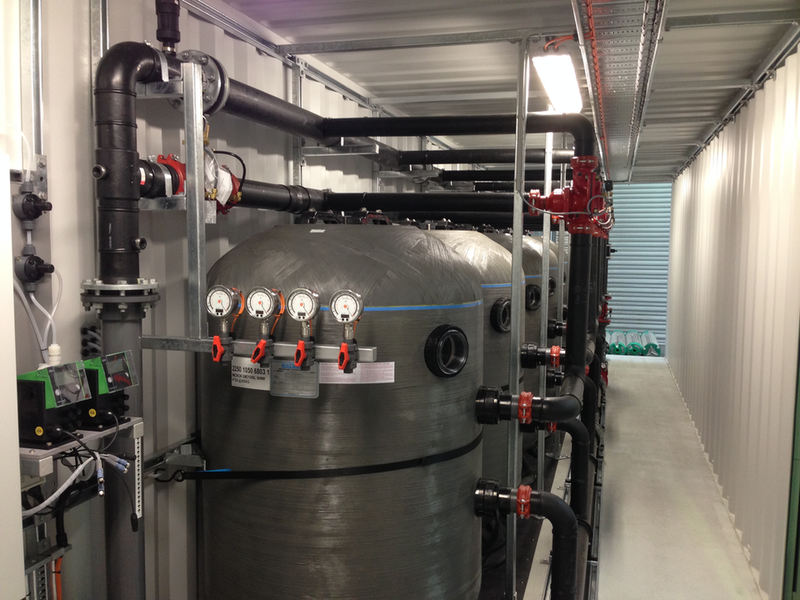
IRON AND MANGANESE BUILDUP:
Build up of iron and manganese results in very high maintenance overheads, loss of production and potentially system failure. DMI-65® efficiently removes dissolved iron to the almost undetectable levels as low as 0.005mg/L and manganese to 0.001mg/L as well as particulate, effectively removing this risk.
REDUCED COSTS:
The total cost of the iron and manganese removal water filtration system is significantly less than alternative solutions, the effectiveness, but relative simplicity, of DMI-65® based systems reduces the upfront capital expenditure on plant complexity as well as the ongoing operational e18xpenditure in chemicals, power and backwash waste water recovery.
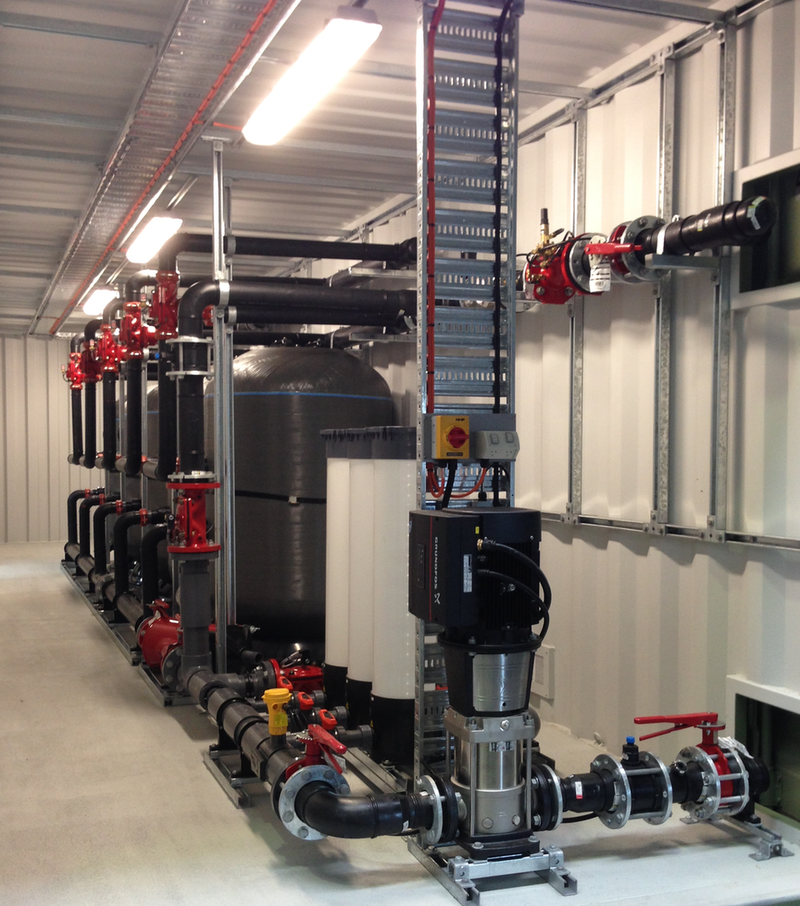
HIGH FLOW RATES:
The infused technology of DMI-65® promotes the highest oxidation rate of any catalytic filtration media. This permits a significantly higher water flow rate to achieve the same level of iron and manganese removal.
DMI-65 can operate at linear filtration velocities up to twice that of conventional media with a corresponding reduction in capital equipment costs.
HIGH LOAD CAPACITY:
DMI-65® also has higher iron and manganese load capacity which can extend the duration of filter runs and the time between backwashing, thereby reducing downtime, operating expense and wastage.
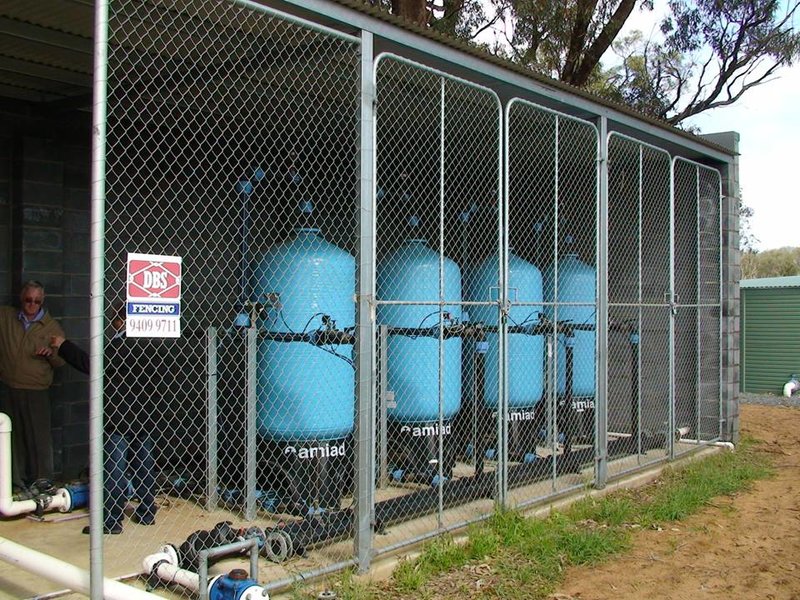
REGENERATION NOT REQUIRED:
The media operates with a continuous injection of sodium hypochlorite at low residual levels (0.1 to 0.3mg/L) which eliminates the need for Potassium Permanganate.
WIDE OPERATING ENVIRONMENT:
Stable and satisfactory performance at pH 5.8 to 8.6 and a maximum operating temperature of 113° F (45°C) reduces the need for investment to alter the operating environment.
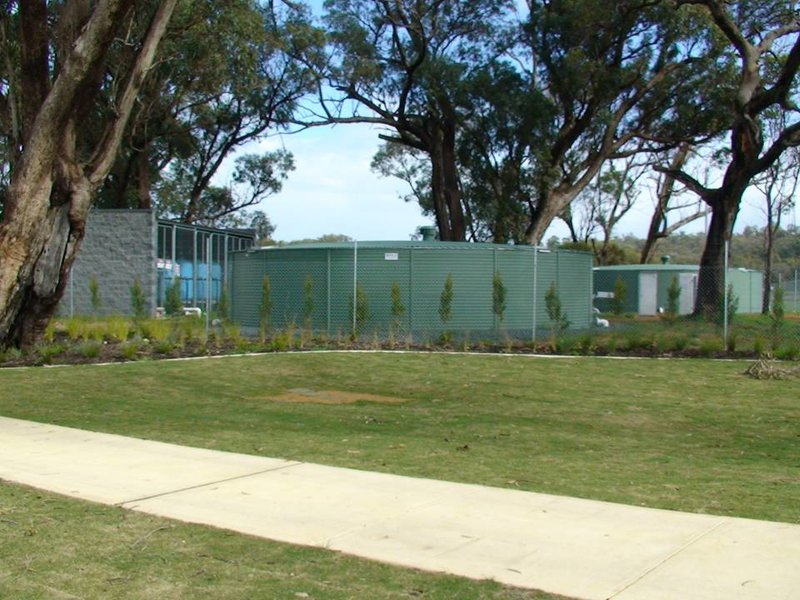
LONG LIFE:
DMI-65® is not consumed in the process giving it an expected operational life of up to 10 years, providing considerable advantages over other processes or media. The media does not display a decaying capacity to do its catalytic work.
Over the 5 to 10 year period, through many backwashing operations of the bed to remove retained solids, an attrition loss of the media occurs by contact between particles and mechanical abrasion.
www.dmi65.com info@dmi65.com +61 1300 303 281