COMPANY INSIGHT
Sponsored by: Quattro Project Engineering
“ENGINEERING PARTNERSHIPS … delivered with efficiency, innovation & energy”
Innovation & solutions within the industry is driven by the requirement for increased safety. Quattro have developed and encouraged a culture to look at existing processes with a view to developing better ways to do it. QPE’s development and launch of a multitude of in house products has contributed extensively, to the progression of the industry.
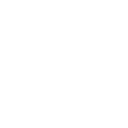
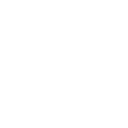
Our experience understanding of industry specific requirements allow us to develop holistic, robust and reliable solutions to meet our client’s needs from conceptual stage through to project delivery. In addition, we have extended our capability into Mine Backfill Design and Rheology technical services through the establishment of our own laboratory to conduct critical test work.
Degrussa125crop
Why are ceramic and urethane linings so important for steel piping in mines?
QPE have invested heavily in our paste capability. Our laboratory allows us to undertake UCS, Slump and viscosity testing of samples to generate robust data for decision-making and system design. We have developed a structured test work methodology which can be tailored to any budget and generate data to enable evaluation of the preferred mix and the associated fill performance. In addition, key elements of data are utilised by our Mechanical Engineering team to develop flow models of reticulation systems and evaluate the estimated operating parameters. These models form the basis of system control and can be calibrated with a control loop in the reticulation during operation. Based on the above, QPE develop reliable paste solutions and provide key data to enable plant and system PLC’s to have a degree of automation over the systems standard operating procedures (SOP).
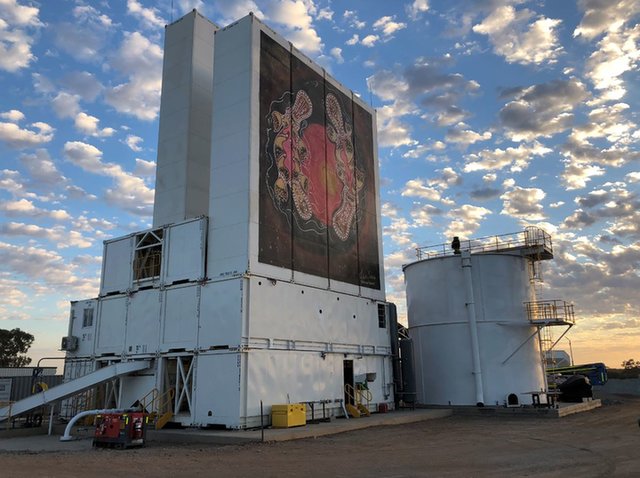
Paste Plant at CSA Cobar
Typical paste systems are subject to conflicting drivers, firstly, to reduce the amount of binder required to achieve strength, which is countered by the requirement to achieve flow from surface to stope. In refining the mix to minimise binder, the solids content is increased to the point where the total system friction head approaches the system gravity head. To allow operators to encroach ever closer to this point, QPE developed a series of proprietary diverters that maintain the full line condition with automated electric over hydraulic
or pneumatic actuation.
QPE’s Engineers develop system flow modelling which predicts the change in pressure across a given segment of reticulation. QPE’s pressure sensing spools, strategically incorporate into the reticulation, can then provide feedback to the plant operator of the actual line pressures and when the pressure drop is approaching a predefined limit. Once the limit is reached the operator can actuate the diverters to a dump position and run a flush sequence.
This sequence effectively divides the systems friction head into segments, whilst maintaining the available gravity head for system flush, which ensures key infrastructure of boreholes and reticulation pipework, can be cleared quickly and effectively to allow operators to minimise binger without jeopardising the fill operation.
More than half of the country’s coal mines are managed by pro-Russian separatist militia. Credit: DmyTo/Shutterstock.
Eero Knuutila is Head of Service Development at Helsinki Airport.
Image courtesy: Helsinki Airport