Q&A with Miguel Angel Peña: Mining innovation with the client at its core
wireless enabled electronic system with 2 way
communication capabilities
read interview
Putting the customer at the heart of everything they do, Enaex is innovating in the areas of robotics and automation to make mining operations safer, more efficient and more sustainable. VP of Innovation, Miguel Angel Peña, explains the increasing importance of innovation and gives an insight into some of the company’s most exciting developments.
Where does innovation fit into Enaex’s vision?
Our central focus is the customer, using innovation as a mechanism to support them solve their main problems. We are interested in understanding our customer issues and needs, to use everything that is in our power to help them. Enaex is proud to design and implement collaborative tailor-made blasting solutions to bring added value new solutions to our customers worldwide, using innovation as a bridge or platform to generate additional solutions. Our company tagline Stronger Bonds, is an external formalization of the work we have been doing since a while.
Humanizing mining has been our company purpose for a couple of years, encompassing safety, better quality of life and having a positive impact in the environment. Along with the agility benefits, among other things, innovation is part of this equation. For example, Enaex Robotics solutions for blasting help in two main ways. First, we take people out of dangerous risk zones, which is an improvement from a safety point of view. Second, in the future we could use teleoperation or automation to have people operating blasting from home, improving quality of life.
What are the applications for robotics?
In robotics we have two main areas of development: open pit and underground.
For example, one of our large multinational customers has an open pit mine with some walls showing certain instability, very close to a natural fracture. In this case, using Enaex Robotics equipment in the pit is a way to avoid having someone down there working, a preventive measure to ensure our collaborators are always working under the safest possible conditions as we consider life a priority.
Cont.
In the close future for open pits, we could also use robotics to operate blasts during the night. That will improve productivity, opening the door to a potential significant increase of blasting per site. Many countries today are having difficulty making their operations more productive, and night shifts, teleoperated trucks and even autonomous trucks will help productivity enormously. At the moment, down the hole, our robotic equipment has the same productivity as a normal human being driving a truck. In a year’s time, I hope that we will achieve the same productivity for priming operations.
Our open-pit applications have provided a lot of know-how, allowing us to accelerate our underground solutions. For deep mining, of around 1 000m or 2 000m down earth, safety is also superb important. Using Enaex Robotics solutions, we will be able to operate underground blasting equipment from the surface. This will make a huge difference: as we improve safety, we will also make mining work environment more appealing.
We can also make more resources available. For example, one of our customers’ underground operations is subject to high seismicity, resulting in a very dangerous work environment. They must often wait for months for seismicity to decrease to use the mine site. By using Enaex Robotics equipment without any collaborators inside, these resources will be available much sooner.
We have successfully managed our open pit remote blasting, planning our first teleoperated underground blasting during last quarter of the year. We are seeking to help our customer achieving a successful underground blasting without any personnel present within the tunnel risk zone, due to the site seismic issues that generate rock burst, through an automatic blasting. Enaex UG iTruck® has the capacity to detect blast holes without human intervention onsite, load the emulsion inside the blast hole, prime and activate an electronic detonator through a remoted-operated blast.
What are some of your newest projects?
Enaex Bright is a digital platform aiming to increase productivity for our clients, while opening an open channel of the collected information with our customers. It has four modules. One module is related to digitalizing the most important information of each site, such as the blast hole dimensions or the product used. The second module is related to maintenance, so we can track each mobile production unit on site, improving the management of the fleet. The third module is related to the information delivered to the client after finalizing down-to-hole services, allowing us to have an open channel of communication with our clients for them to know the exact products information (type, tonnage, etc) being used on their site, eliminating paper and digitise payment. The fourth module facilitates the modelling and optimisation of blasting. We collect information and use artificial intelligence to estimate the quality of the blasting. The platform has already been launched in Chile.
Another solution which is still in development is Enaex GO. It will be a smart track and trace system, enabling more information to be associated with each of our products.
What are the company’s future goals?
Our main goal is to accelerate our complete blasting services solutions in countries where we have just entered through M&A, like South Africa and Australia, providing a complete product portfolio. We also aim to accelerate the entrance of robotics in other main mining regions outside Latin America. We are working with a clear focus of developing added-value solutions for our customers, as we aim to provide support and solutions to their main blasting issues, as a true business partner.
Covid has accelerated recognition of the value of automation. Due to the pandemic restrictions and considering the new global context, our customers experienced a reduction of personnel on site, resulting in certain projects being put on hold. Customers have realised of the benefits teleoperations would represent in their operations, enabling remote blasting not only as a benefit to protect their personnel but as an option to operate from home. The value in digitalising data was also appreciated during Covid, accelerating the demand for innovative solutions such as Enaex Bright.
In the next couple of years, we aim to make operations ten times faster using our Enaex Robotics equipment, resulting in the best productivity option for our customers.
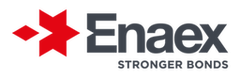
Q&A with Miguel Angel Peña: Mining innovation with the client at its core
wireless enabled electronic system with 2 way communication capabilities
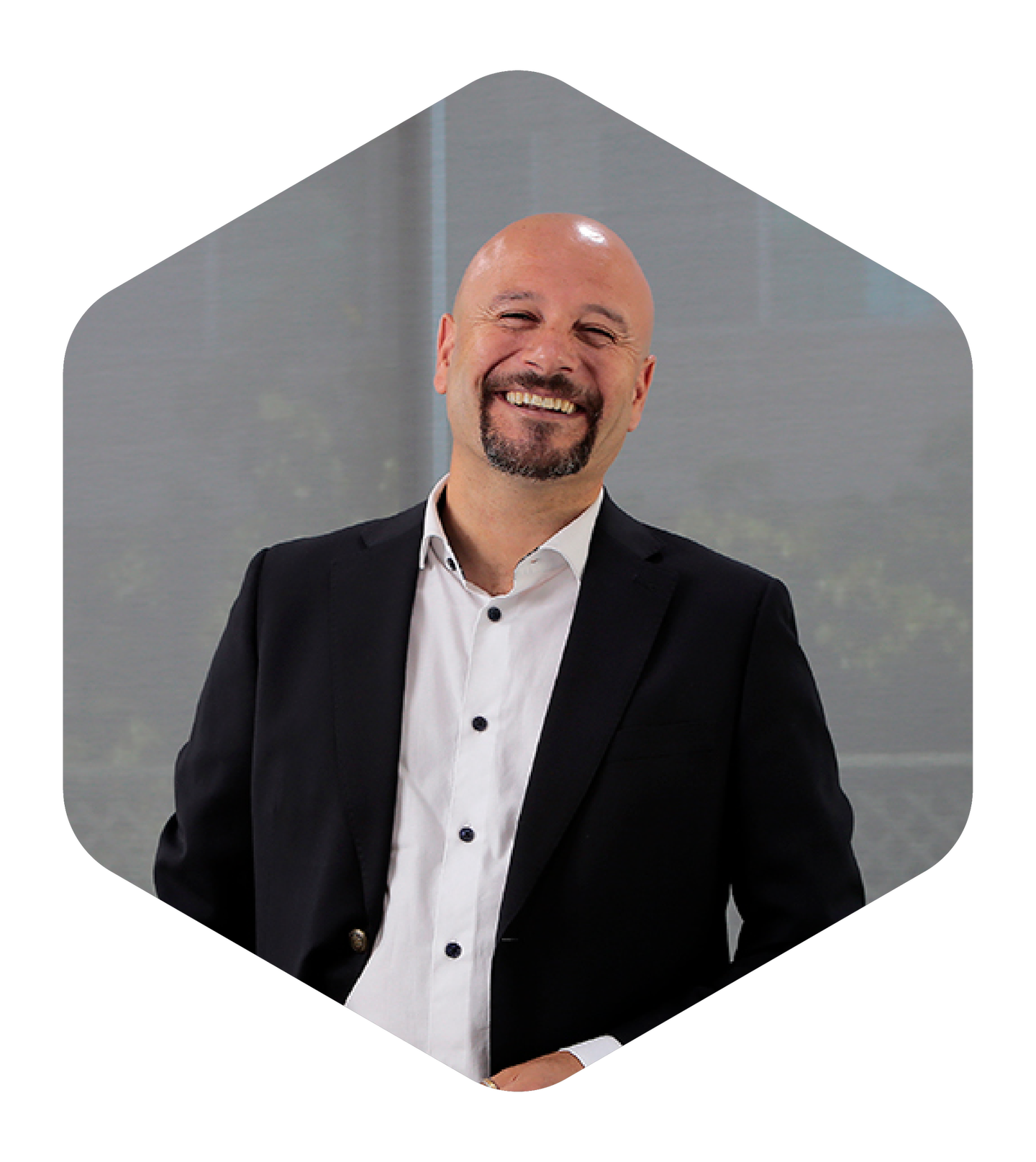

read interview
Putting the customer at the heart of everything they do, Enaex is innovating in the areas of robotics and automation to make mining operations safer, more efficient and more sustainable. VP of Innovation, Miguel Angel Peña, explains the increasing importance of innovation and gives an insight into some of the company’s most exciting developments.
Where does innovation fit into Enaex’s vision?
Our central focus is the customer, using innovation as a mechanism to support them solve their main problems. We are interested in understanding our customer issues and needs, to use everything that is in our power to help them. Enaex is proud to design and implement collaborative tailor-made blasting solutions to bring added value new solutions to our customers worldwide, using innovation as a bridge or platform to generate additional solutions. Our company tagline Stronger Bonds, is an external formalization of the work we have been doing since a while.
Humanizing mining has been our company purpose for a couple of years, encompassing safety, better quality of life and having a positive impact in the environment. Along with the agility benefits, among other things, innovation is part of this equation. For example, Enaex Robotics solutions for blasting help in two main ways. First, we take people out of dangerous risk zones, which is an improvement from a safety point of view. Second, in the future we could use teleoperation or automation to have people operating blasting from home, improving quality of life.
What are the applications for robotics?
In the close future for open pits, we could also use robotics to operate blasts during the night. That will improve productivity, opening the door to a potential significant increase of blasting per site. Many countries today are having difficulty making their operations more productive, and night shifts, teleoperated trucks and even autonomous trucks will help productivity enormously. At the moment, down the hole, our robotic equipment has the same productivity as a normal human being driving a truck. In a year’s time, I hope that we will achieve the same productivity for priming operations.
Our open-pit applications have provided a lot of know-how, allowing us to accelerate our underground solutions. For deep mining, of around 1 000m or 2 000m down earth, safety is also superb important. Using Enaex Robotics solutions, we will be able to operate underground blasting equipment from the surface. This will make a huge difference: as we improve safety, we will also make mining work environment more appealing.
We can also make more resources available. For example, one of our customers’ underground operations is subject to high seismicity, resulting in a very dangerous work environment. They must often wait for months for seismicity to decrease to use the mine site. By using Enaex Robotics equipment without any collaborators inside, these resources will be available much sooner.
We have successfully managed our open pit remote blasting, planning our first teleoperated underground blasting during last quarter of the year. We are seeking to help our customer achieving a successful underground blasting without any personnel present within the tunnel risk zone, due to the site seismic issues that generate rock burst, through an automatic blasting. Enaex UG iTruck® has the capacity to detect blast holes without human intervention onsite, load the emulsion inside the blast hole, prime and activate an electronic detonator through a remoted-operated blast.
What are some of your newest projects?
Enaex Bright is a digital platform aiming to increase productivity for our clients, while opening an open channel of the collected information with our customers. It has four modules. One module is related to digitalizing the most important information of each site, such as the blast hole dimensions or the product used. The second module is related to maintenance, so we can track each mobile production unit on site, improving the management of the fleet. The third module is related to the information delivered to the client after finalizing down-to-hole services, allowing us to have an open channel of communication with our clients for them to know the exact products information (type, tonnage, etc) being used on their site, eliminating paper and digitise payment. The fourth module facilitates the modelling and optimisation of blasting. We collect information and use artificial intelligence to estimate the quality of the blasting. The platform has already been launched in Chile.
Another solution which is still in development is Enaex GO. It will be a smart track and trace system, enabling more information to be associated with each of our products.
What are the company’s future goals?
Our main goal is to accelerate our complete blasting services solutions in countries where we have just entered through M&A, like South Africa and Australia, providing a complete product portfolio. We also aim to accelerate the entrance of robotics in other main mining regions outside Latin America. We are working with a clear focus of developing added-value solutions for our customers, as we aim to provide support and solutions to their main blasting issues, as a true business partner.
Covid has accelerated recognition of the value of automation. Due to the pandemic restrictions and considering the new global context, our customers experienced a reduction of personnel on site, resulting in certain projects being put on hold. Customers have realised of the benefits teleoperations would represent in their operations, enabling remote blasting not only as a benefit to protect their personnel but as an option to operate from home. The value in digitalising data was also appreciated during Covid, accelerating the demand for innovative solutions such as Enaex Bright.
In the next couple of years, we aim to make operations ten times faster using our Enaex Robotics equipment, resulting in the best productivity option for our customers.
Covid has accelerated recognition of the value of automation. Due to the pandemic restrictions and considering the new global context, our customers experienced a reduction of personnel on site, resulting in certain projects being put on hold. Customers have realised of the benefits teleoperations would represent in their operations, enabling remote blasting not only as a benefit to protect their personnel but as an option to operate from home. The value in digitalising data was also appreciated during Covid, accelerating the demand for innovative solutions such as Enaex Bright.
In the next couple of years, we aim to make operations ten times faster using our Enaex Robotics equipment, resulting in the best productivity option for our customers.
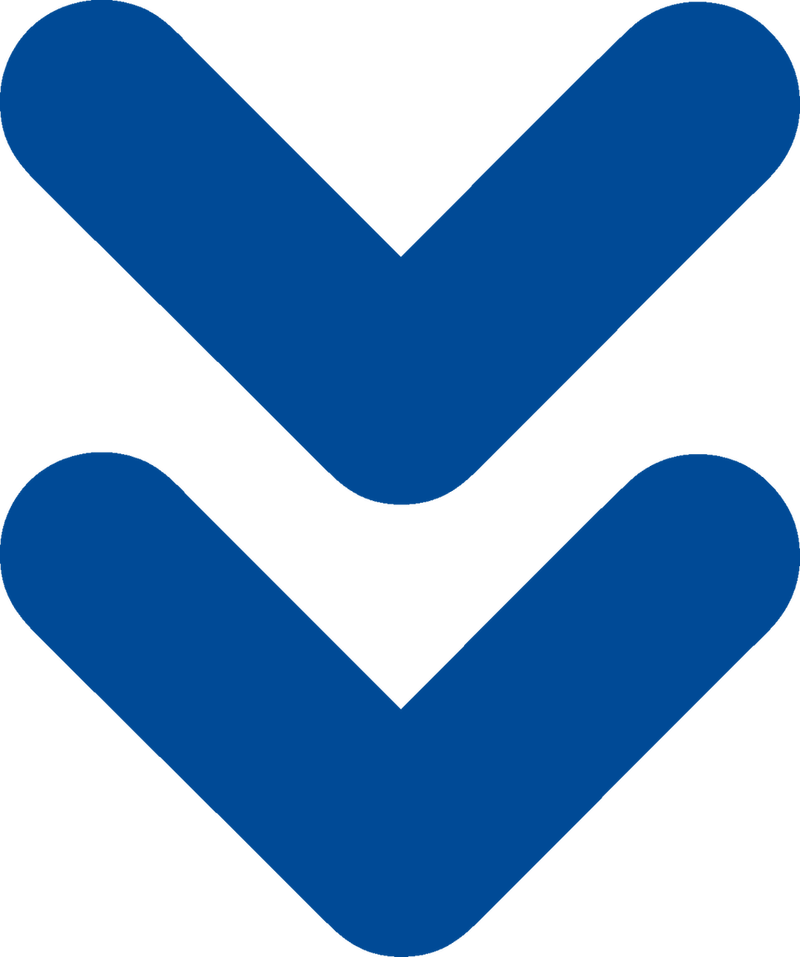