Wireless Monitoring For the
Autonomous Future
The mines of the future save money and reduce downtime on their conveyor systems through the Proactive Real-Time Monitoring of Pulleys and Rollers.
THE NEW WORLD OF WIRELESS MONITORING
DXTA have developed a wireless based monitoring system for conveyor system pulleys and rollers that in real time gives you an early warning of potential component failures. You are provided with a web based dashboard for analysing potential issues and warnings are sent via SMS, email or both
Reduced Downtime
Conveyor downtime directly impacts a company’s bottom line, knowing which pulleys and rollers to replace when scheduled maintenance occurs will reduce downtime due to unexpected failures. The DXTA system will provide a detailed schedule of which rollers to replace and their location.
Real-Time Monitoring
Knowing when a roller or pulley might be going to fail would improve the cost effectiveness of conveyors significantly. The monitoring system runs 24/7 and generates realtime alerts displayed via a traffic light system on a web based dashboard.
Stock Control
The DXTA system will build a list of roller stock codes and their location requiring replacement ensuring that the necessary stock can be available when a scheduled maintenance shutdown occurs.
Proactive Maintenance
By identifying rollers with potential issues the maintenance program becomes more proactive. The DXTA system learns over time what constitutes potential issues allowing roller replacement to be based on actual performance issues rather than how long it has been installed.
Reduced OHS Risk
The DXTA system can reduce the need for employees to expose themselves to OHS risks as the monitoring is done without human intervention.
Data Analysis
All data used to generate the web based dashboard is stored in an industry standard database allowing further analysis and reporting on issues identified. We can also develop interfaces to link directly with clients ERP systems if required.
PO Box 7638, Garbutt, Queensland 4814 | Call Us: + 61 4774 4162 | + 61 407 129 368 | lpozzebon@dxta.com.au
PO Box 7638, Garbutt, Queensland 4814
Call Us: + 61 4774 4162 | + 61 407 129 368
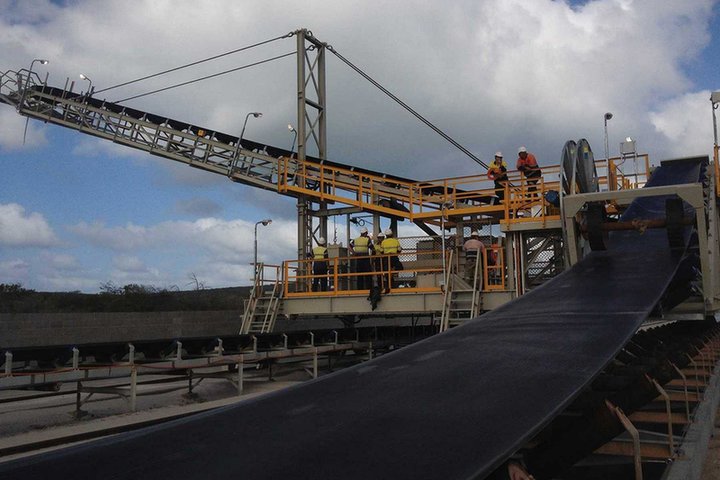
Reduced Downtime
Conveyor downtime directly impacts a company’s bottom line, knowing which pulleys and rollers to replace when scheduled maintenance occurs will reduce downtime due to unexpected failures. The DXTA system will provide a detailed schedule of which rollers to replace and their location.
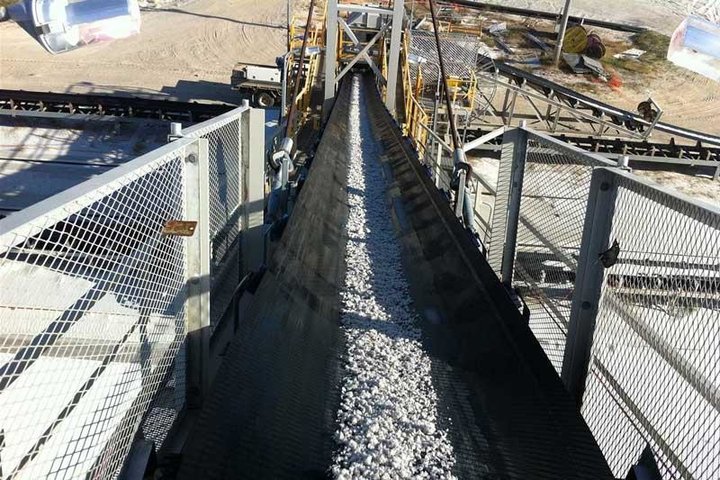
Real-Time Monitoring
Knowing when a roller or pulley might be going to fail would improve the cost effectiveness of conveyors significantly. The monitoring system runs 24/7 and generates realtime alerts displayed via a traffic light system on a web based dashboard.
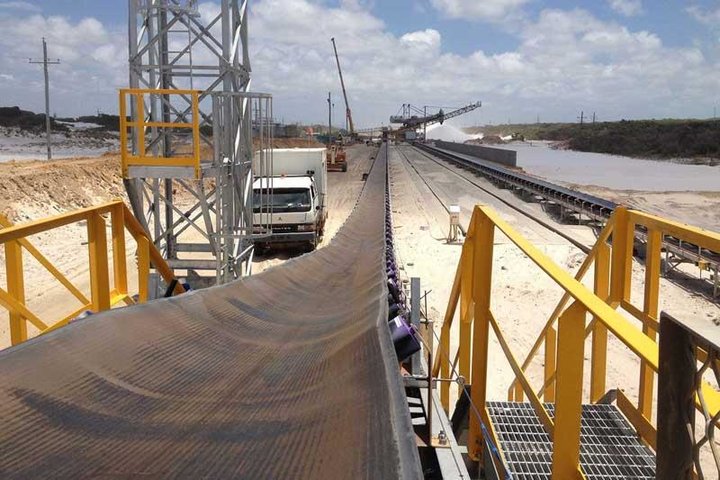
Stock Control
The DXTA system will build a list of roller stock codes and their location requiring replacement ensuring that the necessary stock can be available when a scheduled maintenance shutdown occurs.
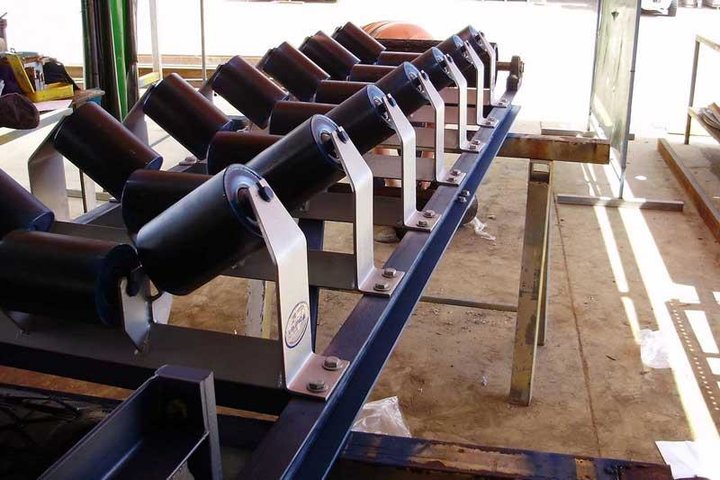
Proactive Maintenance
By identifying rollers with potential issues the maintenance program becomes more proactive. The DXTA system learns over time what constitutes potential issues allowing roller replacement to be based on actual performance issues rather than how long it has been installed.
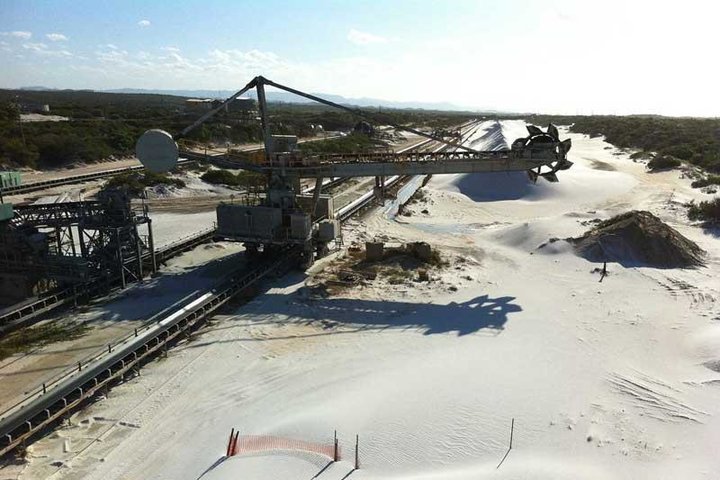
Reduced OHS Risk
The DXTA system can reduce the need for employees to expose themselves to OHS risks as the monitoring is done without human intervention.
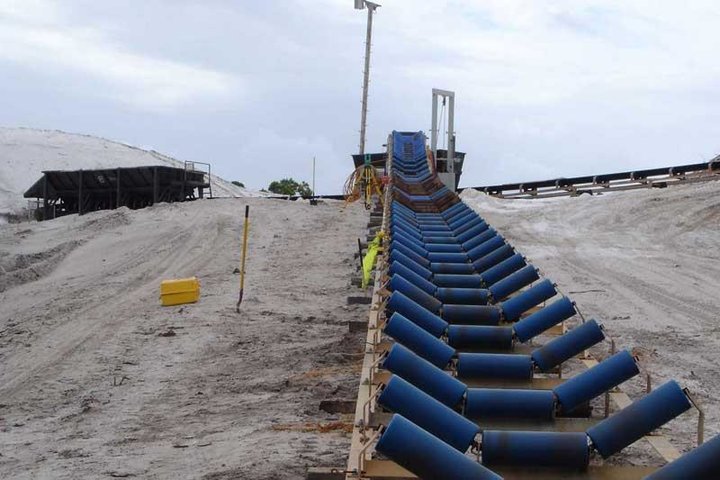
Data Analysis
All data used to generate the web based dashboard is stored in an industry standard database allowing further analysis and reporting on issues identified. We can also develop interfaces to link directly with clients ERP systems if required.