COMPANY INSIGHT
Sponsored by: METTLER TOLEDO
Five Hidden Weighbridge Costs
John Beard from METTLER TOLEDO Australia explains how to avoid the hidden costs associated with weighbridge ownership
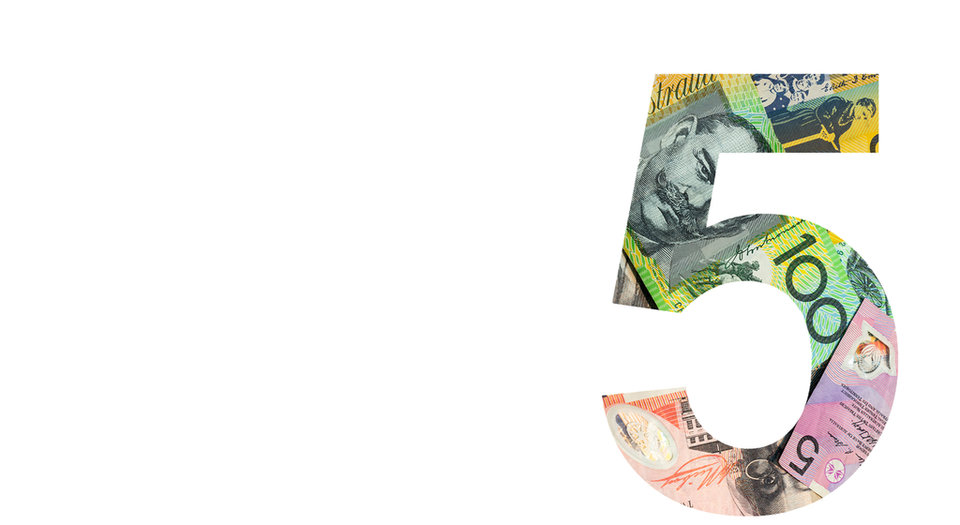
W
ith the ever-changing world economy, businesses are looking for smart ways to manage their operational expenses today to ensure financial security tomorrow. Topics, such as operational excellence and sustainability, are widely discussed in many industries, including the mining industry. However, one area that often is overlooked when cutting costs is weighbridges. However, an educated weighbridge owner knows that there are hidden costs that can be associated with weighbridges. If managed properly, those costs actually can be turned in to huge savings.
1. Reliability
Weighbridges are exposed to extreme conditions brought on by their environment and application, and the mining industry is no exception. These conditions can lead to issues with scale reliability and ultimately downtime, resulting in long lines, lost business and out-of-pocket repair costs. Many facility managers consider those costs to be a normal part of owning a weighbridge, but you can avoid them. As advances are made with each new generation of weighbridge technology, they are becoming increasingly more reliable.
Traditionally the main causes of weighbridge downtime can be attributed to the load cell system and problems brought on by the scales environment. Unfortunately, load cells are an unavoidable piece of equipment necessary for a weighbridge to operate. With typical full-length weighbridges requiring six to 12 load cells, there are many opportunities for something to go wrong. For this reason choosing the right product is important to help avoid hidden costs.
Cables are an important part of any load cell system, connecting the various components and transferring the captured weight readings from each cell finally to the indicator. Cables can contribute to reliability issues and downtime if they are not properly protected from the elements. Products with stainless-steel braided sheathing are available to protect cables from damaging environments and rodents. Additionally, consider a load cell system with detachable cables. Unlike systems with cables that are permanently connected, if damage is done to a single cable it can be replaced quickly and for a fraction of the cost of a new load cell.
Weighbridges are naturally prone to lightning strikes due to their environments. Although most weighbridges have grounding features, when lightning strikes it can cause damage to the load cell system. If your operation is located in an area that frequently experiences severe weather, it would be beneficial to shop for options that offer improved lightning protection.
One of the leading causes of scale breakdowns and poor reliability is junction boxes. Most traditional load cell systems require a junction box. Their function is to connect the cables from each load cell sensor and transmit the weight readings to the terminal for summation. However, the connections made with the junction box can be easily compromised by moisture and corrosion. When a connection with a junction box is compromised, it can cause inaccurate weight readings and breakdowns. While many scale companies have tried to effectively seal junction boxes from moisture, it has been proven over time that this is not possible. Servicing a junction box requires that it is open, and inevitably condensation will get in the box and eventually erode key components. To avoid many of the hidden expenses associated with poor weighbridge reliability, look for load cell systems without junction boxes.
2. Scale Maintenance and Repair
For many operations, a service and repair budget is built into annual maintenance expenses that are to be used throughout that year. Mining operators who use weighbridges in tough environments, require some preventative maintenance measures. Services, such as weighbridge cleaning, health checks and recalibrations, are important to extend the life of a weighbridge and ensure weighing accuracy. Other costs that fall into this category can be considered hidden costs.
Replacing failed load cells is a cost that often gets filed into the category of maintenance and repair. Expenses can range from minor to a sizable bill, and include the cost of parts, labor, travel, mileage and more. Many weighbridge owners consider the expenses associated with maintenance and repair to be unavoidable; however, there are ways to avoid these hidden costs.
Selecting the right load cell system is imperative to avoiding the mounting costs that can be associated with scale maintenance and repair. Traditional analog load cell technology, invented in the 1970s, often falls short meeting the harsh demands of the environments in which weighbridges operate. Fortunately, there are products available that have progressed, providing a superior level of reliability.
With a load cell system that is not prone to break downs, a weighbridge owner will see a decrease in maintenance and repair costs that were once considered unavoidable. As instances of load cell failure decrease, cost of servicing a broken down scale will also decrease. Eliminating those hidden costs further promotes the goal of sustainability and operational excellence.
3. Scale Accuracy, or Inaccuracy
Weighbridge accuracy is a topic that is often overlooked. Many scale owners believe that if their scale is calibrated to be within legal-for-trade tolerances, then that means the weighbridge is accurate enough. However even a small amount of legally acceptable scale inaccuracy can add up to a huge product and profit loss over time. If your operation is working to achieve sustainability and operational excellence, weighbridge inaccuracy is a hidden expense that should be discussed.
Even a small to mid-size operation can experience huge losses with a seemingly small discrepancy in accuracy. Most calibration tests only set scales back to legal-error tolerances, and not "0" error. Refer to the table below for an example of how these errors can add up for a mining business.
Although many companies tend to focus on the structure of the weighbridge, weighbridges accuracy is most heavily dependent on the load cell system of the scale. For this reason, it is important to consider both weighbridge and load cell system for the best results when cutting hidden inaccuracy costs from your operation.
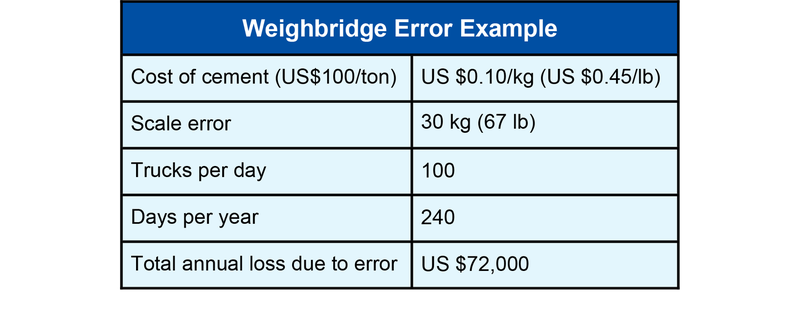
4. Total Cost of Ownership
The total cost of owning a weighbridge can be considered one of the most extreme hidden expenses. They are costs that happen gradually over time, and often go unnoticed by the weighbridge owner. When summed together at the end of the weighbridge's life, these costs can tell you what you really paid and if you got the deal you were expecting.
Many weighbridge owners and buyers focus on the initial purchase price of a scale as the most important criteria in their decision. However, the initial cost often does not reflect what the total cost of owning the scale will be. Factors such as reliability and accuracy, as well as longevity, play the biggest role in determining the final cost.
Reliability – There are many hidden costs that can stem from poor scale reliability. Breakdowns lead to expenses including replacement parts, service costs and the cost of lost business. When these expenses are included in the total sum of costs at the end of a weighbridge's life, they will dramatically affect the resulting numbers.
Accuracy – When we discuss the concept of scale accuracy, many times business owners are thinking of the impact it will have on the present. However, it is over the life of a scale that the cost of inaccuracy can have the biggest impact.
Longevity – Often overlooked when shopping for a weighbridge is the proof of longevity. It seems like a simple concept; the longer the scale will last, the lower the total cost of ownership will be. However, many scale providers lack the information to demonstrate how long their scale will truly last before needing replaced. A purchaser should request proof of longevity, through both testing and field experience, to ensure they are getting a quality scale.
Considering those three points before making a weighbridge purchase can help you significantly reduce the hidden costs associated with total cost of ownership.
5. Warranty
A weighbridge warranty is another sneaky hidden cost that can show its true colors over time. Here is a list of points to look out for when examining a company's warranty:
- What is really covered and how long? Make sure to read the fine print. Many warranties sound great, but upon thorough examination, gaps in coverage are revealed.
- Look for service coverage of labour, travel and mileage. Some warranties only cover those for a short time. Those hidden costs can add up quickly.
- What is the hidden meaning of the warranty? Poor warranty coverage can often be related to lack of confidence in a product. Seeking out a company with a great product AND strong warranty can help to reduce hidden costs in the future.
A weighbridge is a significant investment that can come with significant hidden costs. Fortunately, there are many ways for your mining operation to avoid these, helping to contribute to the overall sustainability and operational excellence of the company.
Contact information
METTLER TOLEDO
Offices in all major states across Australia
Tel: 1300 659 761
Email:info.mtaus@mt.com
