THE TOP 5 REASONS WHY LINER BOLTS FAIL AND THE 4 PROCESSES WE DO THAT ELIMINATE BOTH FAILURES AND THE REQUIREMENT TO RE-TORQUE THE BOLTS.
1. The conditions are always difficult; dirt, rough interfaces, damaged bolt holes. This is a tough environment that doesn’t behave anything like workshop or laboratory trials.
2. Embedment of mating components after start-up causes loss of bolt elongation. That’s the primary reason that the
re-torque process is employed.
3.
Interaction between Grate and Pulp lifters.
4.
Short clamp length of Pulp Lifter and Shell (belly) bolts.
5.
Selection and application of thread lubricants.
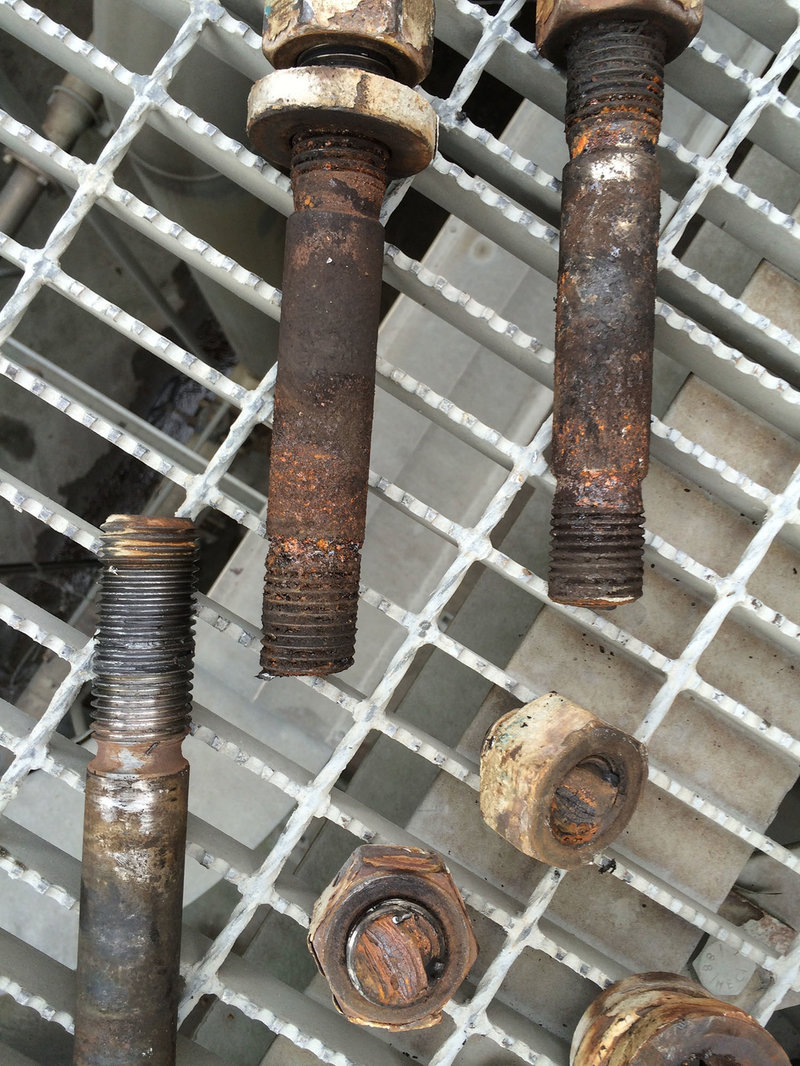
WHAT WE DO TO ELIMINATE FAILURES & THE RE-TORQUE
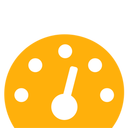
1. Gather bolt stress measurements to determine what the real performance of your torquing system and procedures are.
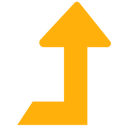
2. Determine how great the in-service relaxation is at each stage of the process.
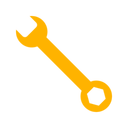
3. Design bespoke bolt torquing systems to minimise weight, improve safety and reduce time.
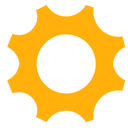
4. Use the collated data to make the changes to the process that eliminate the need to re-torque.
Many mines experience un-planned Mill shutdowns and undertake a process of re-torquing 24-48 hours after start-up to reduce the risk of this. This is costly and reduces throughput.
Overview
We have been providing complete bolting solutions for over 29 years to the Mining, Refining, Hydrocarbon, Power Generation, Marine, Motor Vehicle, Construction and Fairground Industries.
The foundation of our knowledge base has been built by measuring the actual bolt tension (not torque) achieved by any tightening method. This has given rise to a knowledge base that has driven the solutions that we now provide, the two key factors are:
- Ultrasonic Bolt Tension Measurement
- Joint Analysis & Management
Discussion
The process of re-torquing after a re-line is very common. It has been a necessity to reduce the number of failures. In order to find the solution we first had to fully understand all the contributing factors.
ROOT CAUSES OF FAILURES
Liner bolts fail (break or loosen off) for several reasons, but our extensive experience demonstrates that these can be eliminated if the pre-load is correct. Fatigue failure is the most common failure; this is almost invariably due to pre‐load that is too low. The reasons for this can be divided
into three groups: inadequate original tension, inconsistent tension and high relaxation.
Pre-load too low
The interfaces between the bolt, liner & shell are rarely smooth or machined, consequently, the friction is greater than standard calculations consider, this results in low average bolt tension.
Consistency
Consistency is a bigger factor than most realize. The relationship between torque tightening and bolt tension in good conditions is generally regarded as +/- 25%. Add rough surfaces, interaction and short clamp length to diameter ratios and this becomes significantly higher. Our experience is that the variation is often +25% - 100%; (it is rare when we measure all bolts that we don’t find at least one that is completely loose).
High relaxation
We have found that the relaxation on liners is particularly high. The mating surfaces (being cast and forged surfaces) between the liners and bolts are rough. Added to this the tapered engagement multiplies any relaxation. Any small embedment of high spots will be multiplied by the slope angle. By way of an example if 0.1mm embedment occurs on a 1:4 taper that will result in 0.4mm in lost elongation. That is a likely scenario when both sides of the slope are considered.
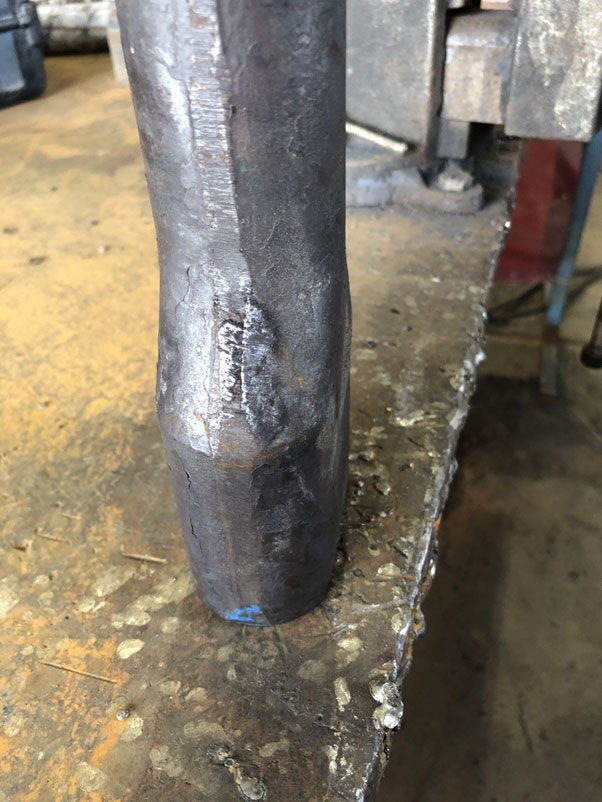
OUR SOLUTION
To eliminate this we measure and adjust every bolt to precisely the required bolt pre-load. Many companies fear that this will slow down the process but because our people do this constantly they are very quick and we reduce the time taken.
Preparation – prior to re-line start
- Calculate allowable tension for the Bolts
- Determine allowable stresses for mating parts
- Set up ultrasonic data files
- Measure bolt reference lengths
During re-line
- Allow re-line crew to tighten 1st set/row of bolts
- Measure residual tension
- Calculate average tension, review and adjust tooling pressure settings
- Re-test on subsequent rows
Using cassette-type torque wrenches with special engineered reaction arms we can place our transducer on the bolt end whilst tightening. We then control the final bolt tension to a much better accuracy (within 3%) and to a higher level.
PROVEN RESULTS
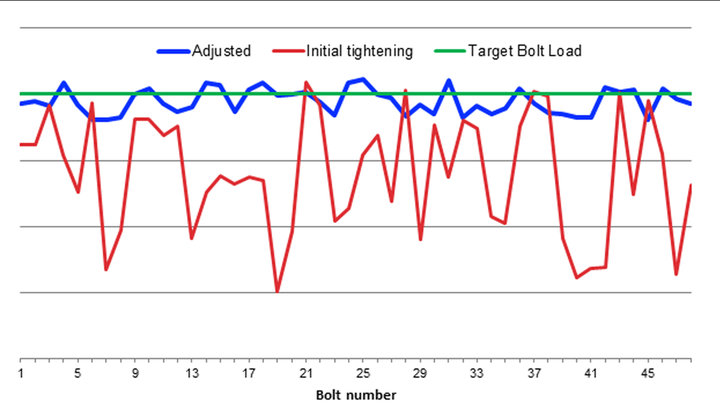
These unadjusted results show the normal variation that torque tightening generates. The average is well below the required pre-load. The variation is + 5% / -75%, which is consistent with other work we have completed (many are worse).
The Blue line is the final adjusted figure that results in the elimination of failures and the re-torque process.
We have 30 year’s experience with the technology and 13 years specifically working on Mill Liner bolts. We are confident that we can both eliminate failures and remove the re-torque process.
In most cases the return on investment has a ratio of more than a 10:1.